Oil Refinery
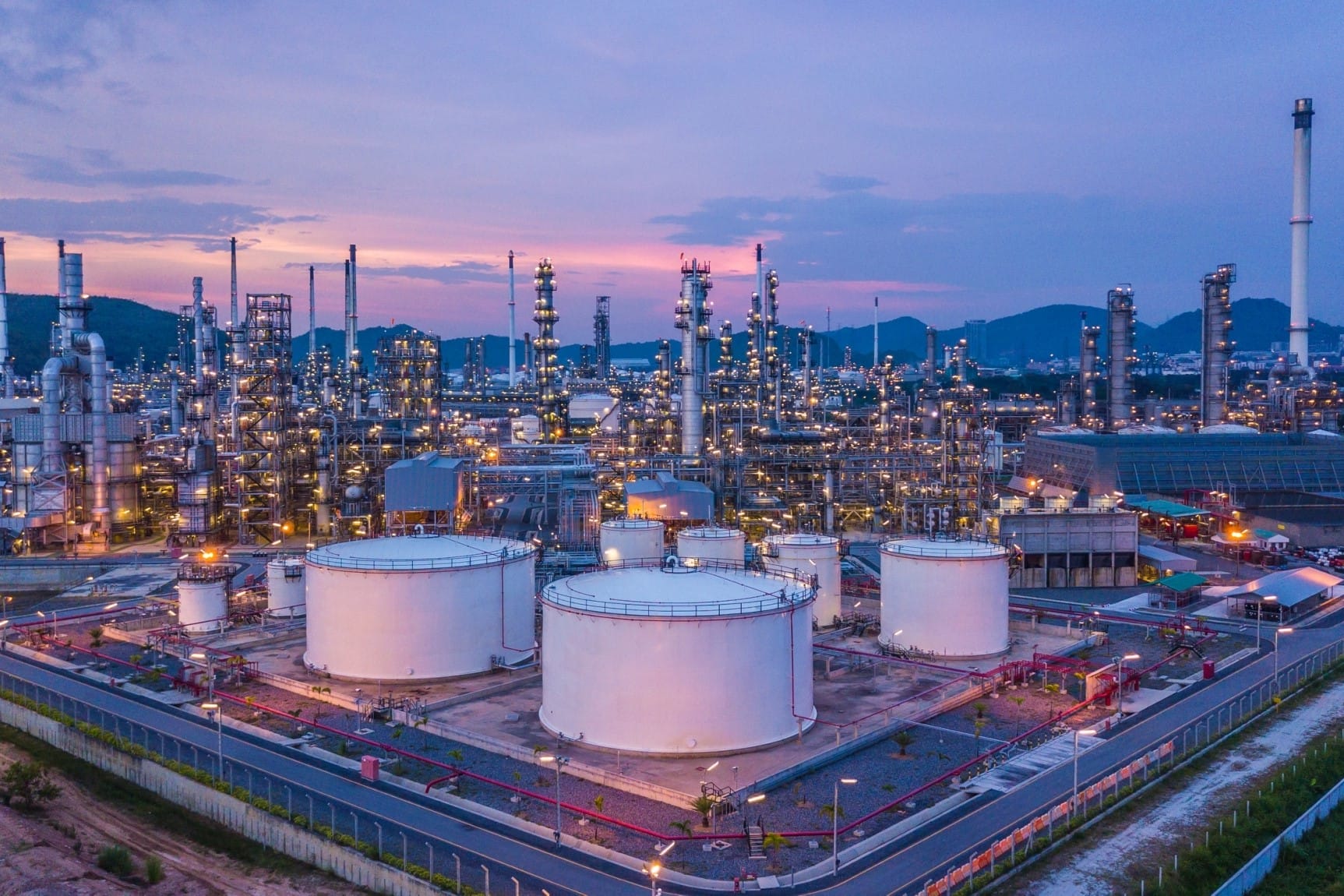
Thai Oil Public Company Limited
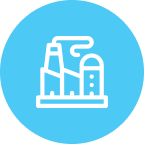
Our Business
Steadily evolving over 60 years, Thai Oil Plc (Thaioil) has transformed from a small refinery with a capacity of 35,000 barrels per day into a complex refinery capable of processing 275,000 barrels per day, producing a diverse range of products, including refined fuels, petrochemicals, and base lubricating oils. Thaioil refinery is designed to maximize value from its production processes, enabling it to adjust the output of finished petroleum products according to market demand while maintaining high flexibility in sourcing raw materials and crude oil from different suppliers.
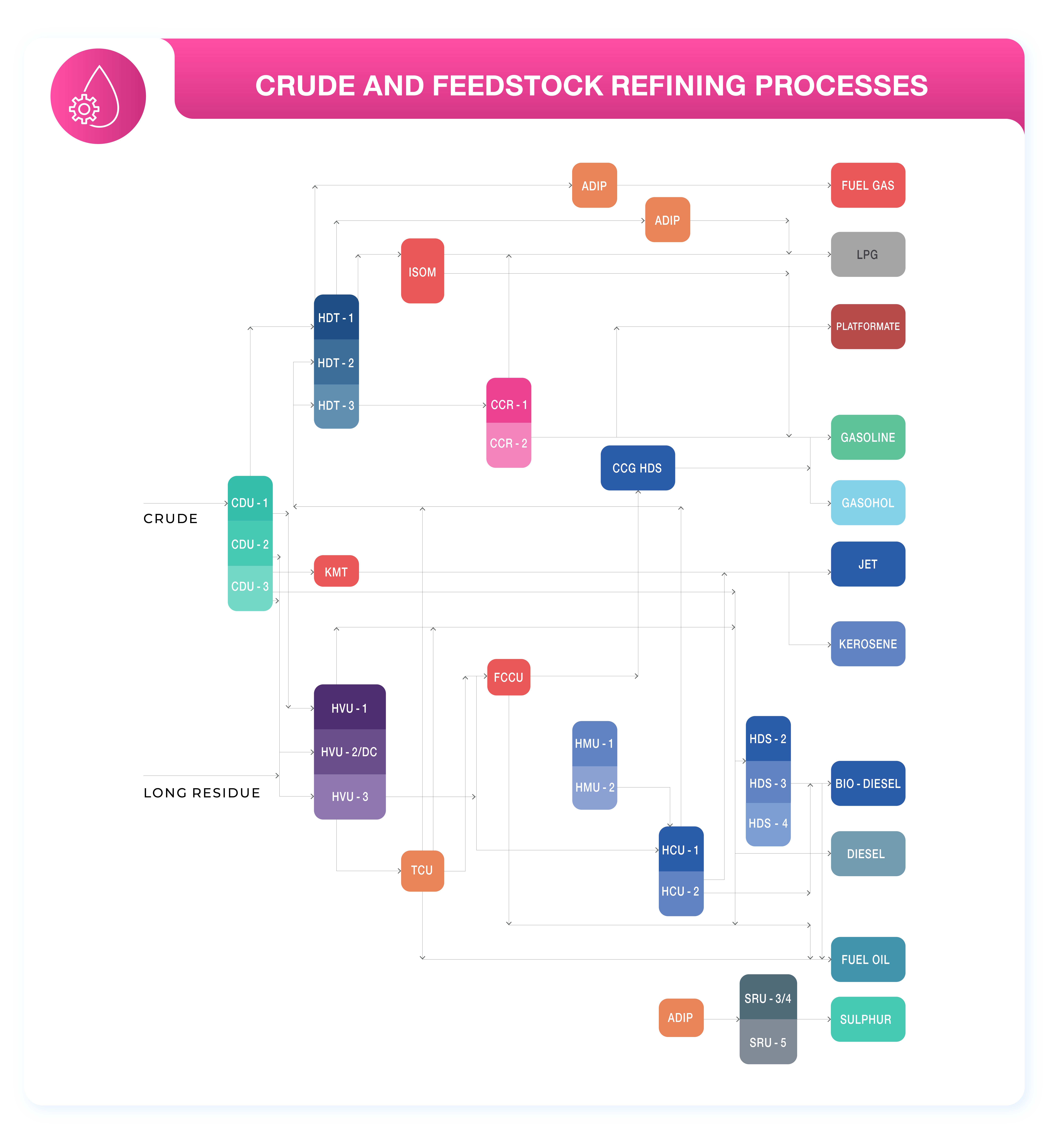
Today, Thaioil refinery has a petroleum refining capacity of approximately 12,000 million liters per year or about 21% of the nation’s overall refining capacity and capable of meeting the domestic demand for petroleum at 35%. Thaioil refinery has been designed to create maximum value from the production system. As a complex refinery, the refining process involves various steps that take place in the crude distillation units, the upgrading units, and the quality improvement units, that make Thaioil becomes one of Asia-Pacific’s leading producers of high quality petroleum products. It also allows for flexibility in using raw materials or crude oil from various sources, and in adjusting the production level of each type of petroleum product to be in line with domestic demand.
Commercial operating date
1961
Business Type
Complex Refinery
Capacity
275,000
*Barrels per day
Products
Vel pretium dolor tellus id purus felis tellus cursus. Amet turpis vel enim aliquet maecenas. Egestas nulla urna suspendisse cursus aliquam mauris facilisis.
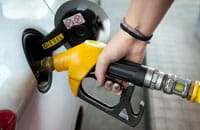
Gasoline
Gasoline is a widely used fuel for cars and motorcycles. Thaioil produces Euro V standard gasoline to comply with government regulations, which involve changes to oil product specifications, including a reduction in sulfur content from 50 ppm to a maximum of 10 ppm. This change decreases emissions of sulfur oxides (SOx), carbon monoxide, and nitrogen oxides. Additionally, the amount of benzene, a known carcinogen, has also been reduced.
Thaioil also produces gasoline base (G-Base), which can be blended with 10%, 20%, and 85% ethanol to create gasohol E10, E20, and E85, respectively. The company primarily produces and distributes gasoline with an octane rating of 95, G-Base 95, and G-Base 91 for domestic consumers.
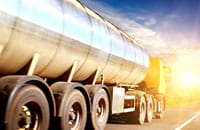
Diesel / Gas Oil
Diesel fuel is used in diesel-engine vehicles, trucks, tractors, passenger boats, fishing vessels, trains, and industrial plants. Currently, Thaioil produces diesel according to Euro 5 standards, which helps reduce emissions of sulfur oxides (SOx), carbon monoxide (CO), nitrogen oxides (NOx), and black smoke into the atmosphere. This also contributes to smoother engine operation. Additionally, the company focuses on distributing base diesel and high-speed diesel blended with approximately 7% and 20% biodiesel for domestic consumers.
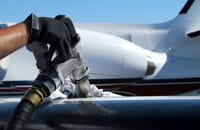
Jet Fuel
Jet fuel is the type of fuel used in jet aircraft and is divided into two categories: commercial jet fuel (Jet A-1), which is used for passenger or general commercial aircraft, and military jet fuel (JP-8), which is used in military activities such as fighter jets and combat aircraft. JP-8 has special properties that enable military aircraft to operate at high speeds.
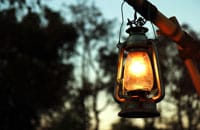
Kerosene
Kerosene is similar to jet fuel and is currently used as a heating fuel in cold regions to warm homes, as well as for cooking purposes.
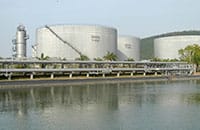
Fuel Oil
Fuel oil is a type of industrial fuel, and Thaioil’s fuel oil is divided into 3 grades:
- Fuel Oil A (FOA): This transparent fuel has a low viscosity of up to 80 centistokes at 50°C and low sulfur content, making it clean and soot-free. It is suitable for use in clean-fired equipment, such as that used in tile manufacturing.
- Fuel Oil C (FOC): This fuel has a moderate viscosity of up to 180 centistokes at 50°C and a sulfur content of 2% or less by weight. It is commonly used in medium to large factories to power engines or steam turbines for electricity generation, as well as in kilns and furnaces for metal melting and cement production.
- Bunker Fuel: This high-viscosity fuel has a viscosity of up to 380 centistokes and is used to power ocean-going vessels. Its sulfur content can be a maximum of 3.5% or 4.0% by weight.
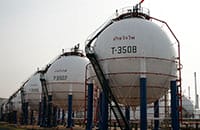
Liquefied Petroleum Gas (LPG)
Liquefied petroleum gas (LPG) is a type of gas that has been liquefied for easier storage and transportation. It is used for cooking, as well as in vehicles and industrial facilities, and serves as a feedstock in petrochemical plants. LPG consists of 60% propane and 40% butane, with sources including refineries, gas separation plants, and imports.
Production processes of petroleum products from crude and other feedstock
The oil refining process is a process where hydrocarbon molecules in crude are distillated into higher value petroleum products.
Individual refineries have different designs on refining ability for crude and other feedstock into assorted products of market needs. The factors deciding which methods and capability of refining are the quality of the crude and types of distillation units. As a rule, crude is grouped into light to heavy by its density from low to high, and sweet to sour by its sulfur content from low to high.
Thaioil Refinery is a complex refinery, housing processes capable of converting low-priced feedstock into premium products. Below is how our processes work.
Oil refining fundamentals and overview
Fractionation occurs in the Crude Distillation Unit (CDU). Crude from storage tanks goes into the CDU and is heated to about 350 degrees Celsius with heat exchangers and fired heaters. The resulting components proceed to the Fractionation Tower, where segregation occurs, depending on boiling points. A portion of the crude evaporates toward the top of the Fractionation Tower, condensing into various distillates, including LPG, naphtha, kerosene, and diesel. The rest of the crude, called residue, emerges at the bottom of the Fractionation Tower. The distillates then enter further processes for further quality improvement and value addition.
Distillate treatment consists of processes designed to remove contaminants, including nitrogen and sulfur compounds. Treatment also improves physical properties, including thermal stability and color stability, to transform distillates into products of greater purity and market quality. Often, these processes rely on catalytic reactions. Catalysts are different in physical & chemical properties depending on the treated distillates. For instance, to treat kerosene, liquid catalysts are needed to accelerate the process; on the other hand, to treat naphtha in the Hydrotreating Unit and diesel in the Hydrodesulfurization Unit, solid catalysts are needed along with hydrogen under high temperatures and pressure.
Since the naphtha derived from the CDU contains low octane numbers along with unsuitable quality for gasoline blending, it undergoes a process to split it into light naphtha and heavy naphtha, which then proceed to different treatment units. Light naphtha proceeds to the Isomerization Unit (ISOM) to raise the octane number from 65-70 to 88-89, which contain no aromatics contaminants, thus making it suitable for blending into low-aromatics gasoline. On the other hand, heavy naphtha proceeds to the Continuous Catalyst Regeneration Unit (CCR) to raise its octane number from 40-50 to 102-103.
The residue from the CDU, commonly termed long residue, enters the High Vacuum Unit (HVU), where Vacuum Gas Oil or VGO (a type of diesel) is distillated from the short residue inside the Fractionation Tower under high temperature and vacuum.
VGO is then fed into the Fluidized Catalytic Cracking Unit (FCCU) at elevated temperatures to crack molecules into high-octane gasoline and diesel. Out of this process, coke forms on the catalysts. To revive these catalysts and reuse them, the coke is burned in the Regenerator unit. An option is to feed light residue into the Hydrocracking Unit (HCU) under high temperature and pressure to crack the molecules and improve their quality to high-value White Oil, namely naphtha, kerosene, and diesel.
As for the short residue derived from the HVU, it proceeds to the Thermal Cracking Unit (TCU) for quality improvement up to the market-dictated values with a process under a high temperature – high pressure environment. Emerging is residue with lower viscosity plus some gasoline and diesel. Thaioil has planned, however, to stop TCU operation once it has to produced 0.5-percent-weight sulfur residue consistent with the International Marine Organization (IMO) standard, since the quality of the TCU residue is not suitable to produce such product. The key objective of the residue conversion process is to lower the volume of low-quality residue while raising the volume of white oil products, including gasoline and diesel, which have premium market values and increasing flexibility for choosing various crude types. Finally, such residue conversion process also enhances gross refining margins over hydro-skimming refineries.
As a rule, a complex refinery yields assorted middle distillates commonly used for fuel blending, thus giving rise to various combinations for premium products. Nevertheless, each product need to be blended with precision, additives & dyes injection to meet market need and product standards. Thaioil currently uses in-line blending for blending gasoline and diesel, leveraging a computerized system of blending ratio control in parallel with online analysis for controlling product quality. This efficiently modulates proportions to yield products meeting quality requirements. For Fuel oil, it is blended by batch blending.
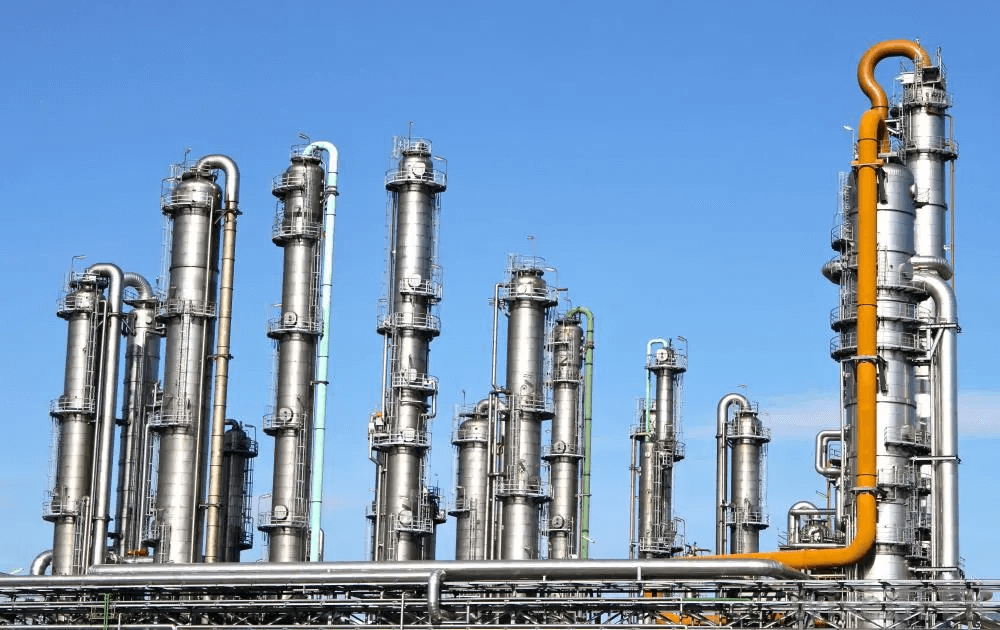
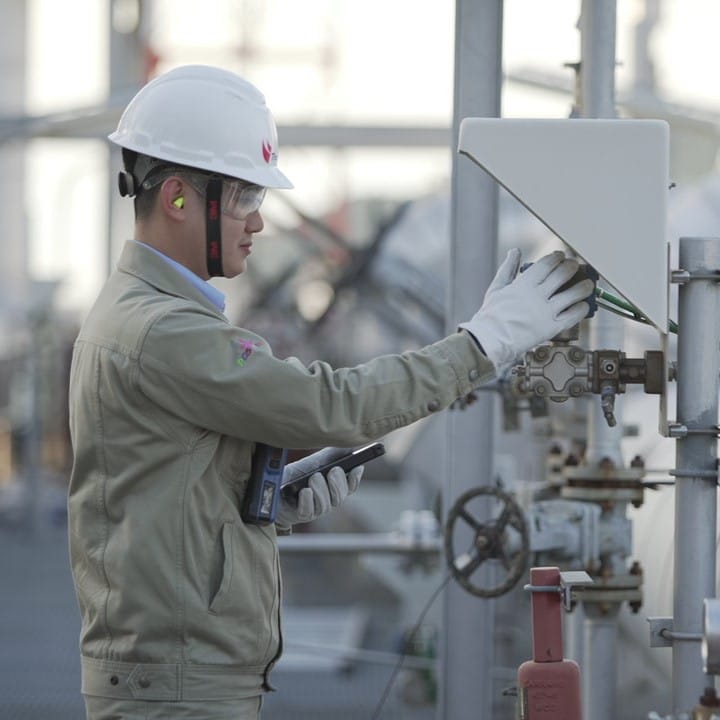
The key objective of the refinery business is to maximize returns from its refined products by optimizing crude and feedstock selection as well as utilizing the proper and efficient refining processes.
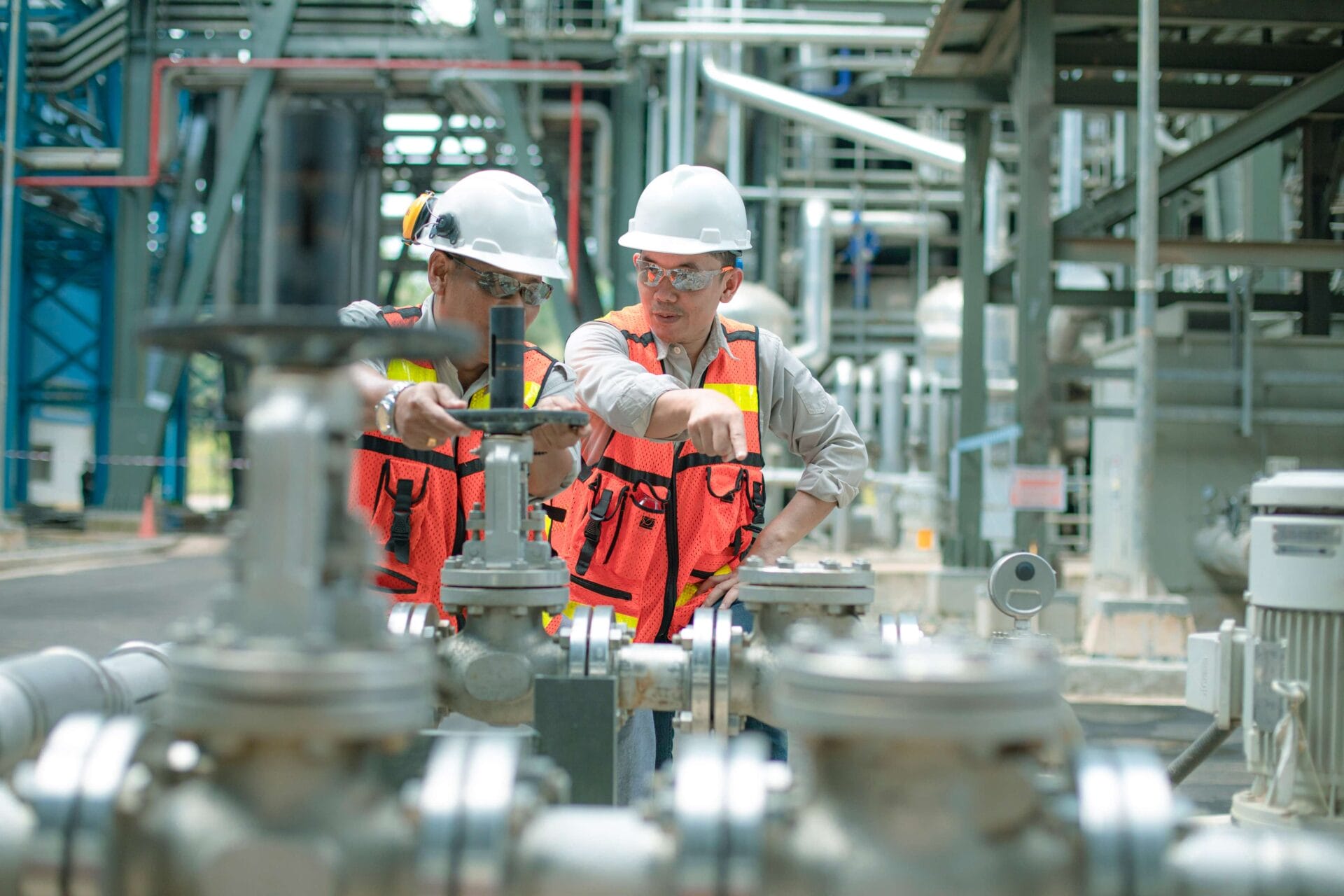
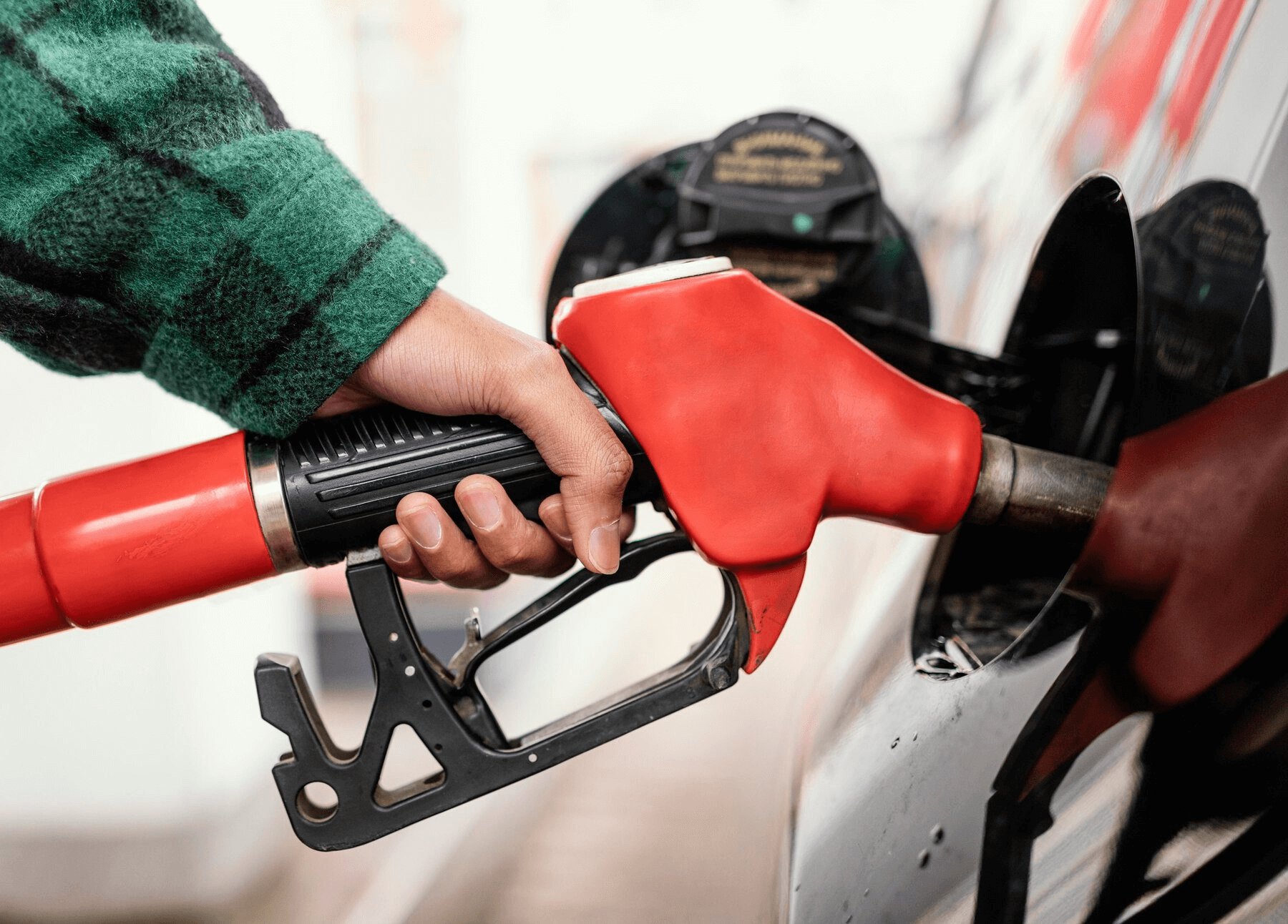
The main refined products consist of LPG, Unleaded Gasoline (ULG), Gasohol, Mixed Xylenes, Jet Fuel, Diesel, Fuel Oil and Bitumen. Gross Refining Margin can be estimated from the difference between the total refined products value and the total cost of intake together with the cost of purchased utilities.
A Simple Refinery is a Hydroskimming refinery, with no heavy oil upgrading units. Refined products from a Simple Refinery are derived directly from crude and feedstock selected. On the other hand, a Complex Refinery possesses a variety of heavy oil upgrading units that can convert lower value Fuel Oil and Bitumen into more valuable light distillate products such as Gasoline, Jet or Diesel. Hence, products from a Complex Refinery contain higher portion of valuable light distillate products and lower Fuel Oil and Bitumen. Gross Refining Margin of a Complex Refinery is more attractive than a Simple Refinery since it yields in more higher value distillate while being able to utilize lower cost crude and feedstock.
The benchmarks of the refining industry include the Nelson Complexity Index (NCI, which measures refining process complexity), gross refining margin, utilization rate, operational availability, and energy intensity index (EII).
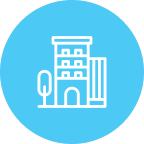
General Information
Thaioil engages in the business of refining and distributing refined products with leading efficiency in the Asia Pacific region.
Acronym
TOP
Registration Number
0107547000711
Type of Business
Complex Refinery
Registered Capital
22,338,355,660 baht, made up of 2,233,835,566 common shares
Value per Share
10 baht
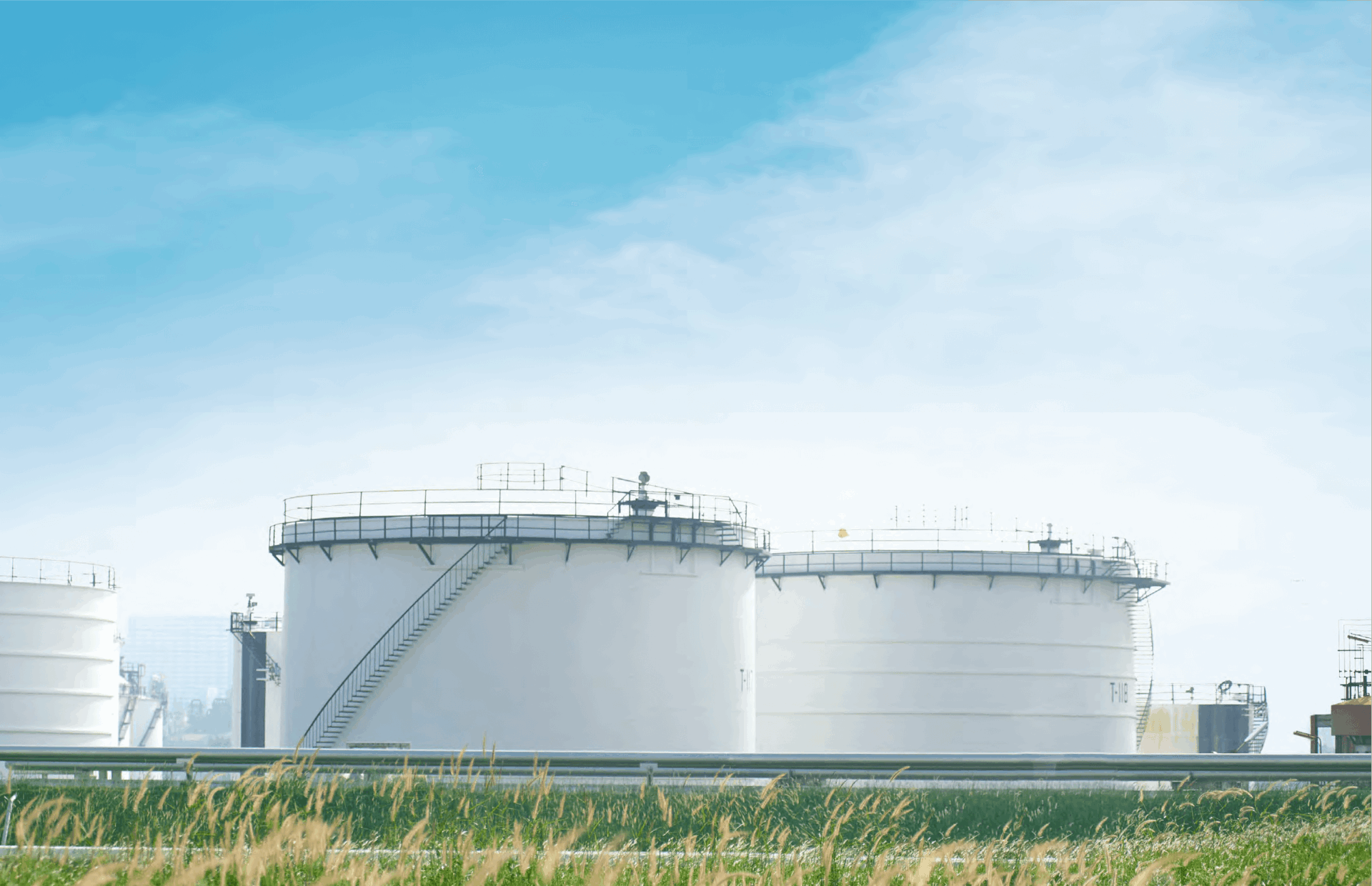
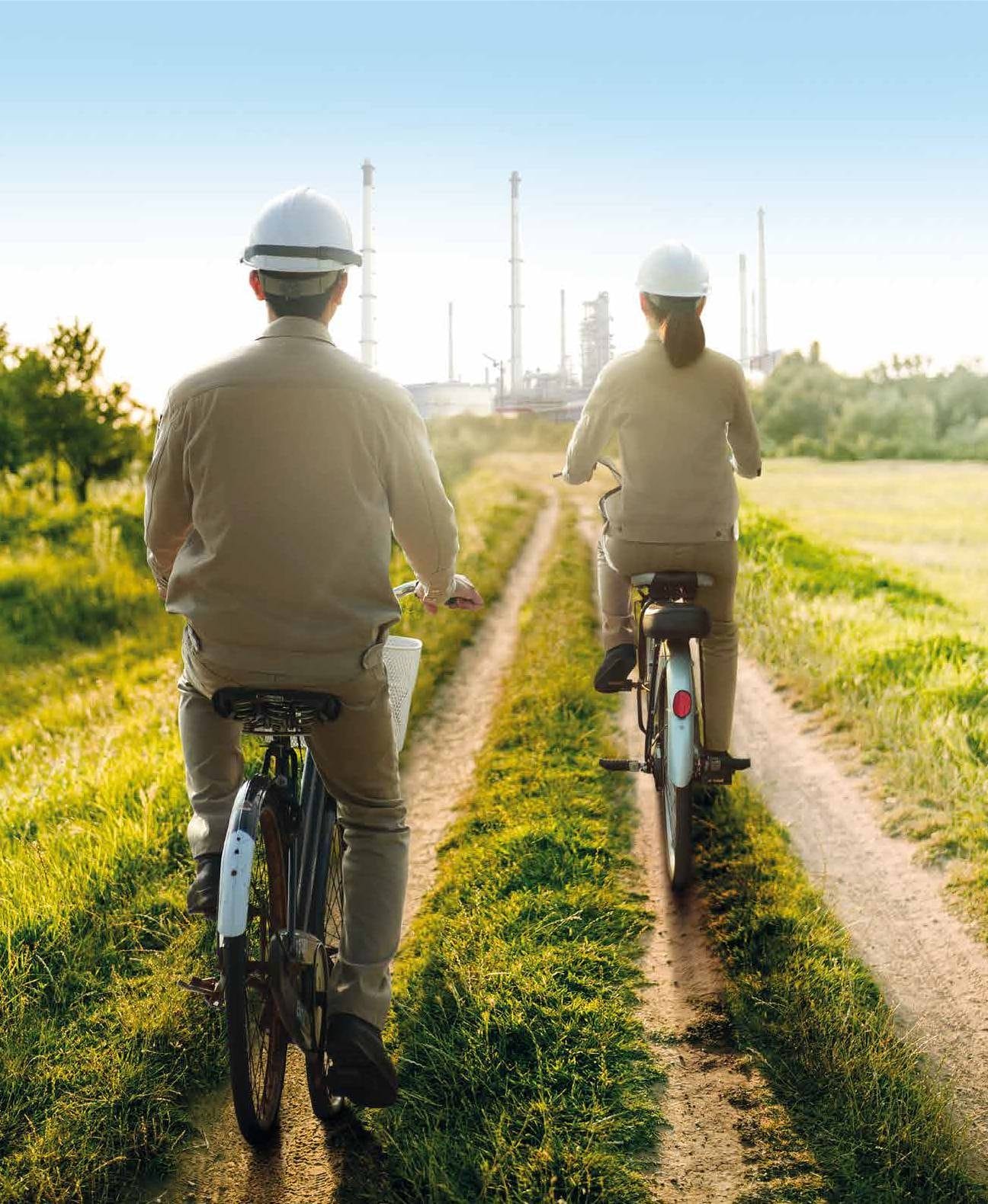
Contact Us
Thai Oil Public Company Limited
Lorem Ipsum is simply dummy text of the printing and typesetting industry. Lorem Ipsum is simply dummy text of the printing and typesetting industry. Lorem Ipsum is simply dummy text of the printing and typesetting industry.
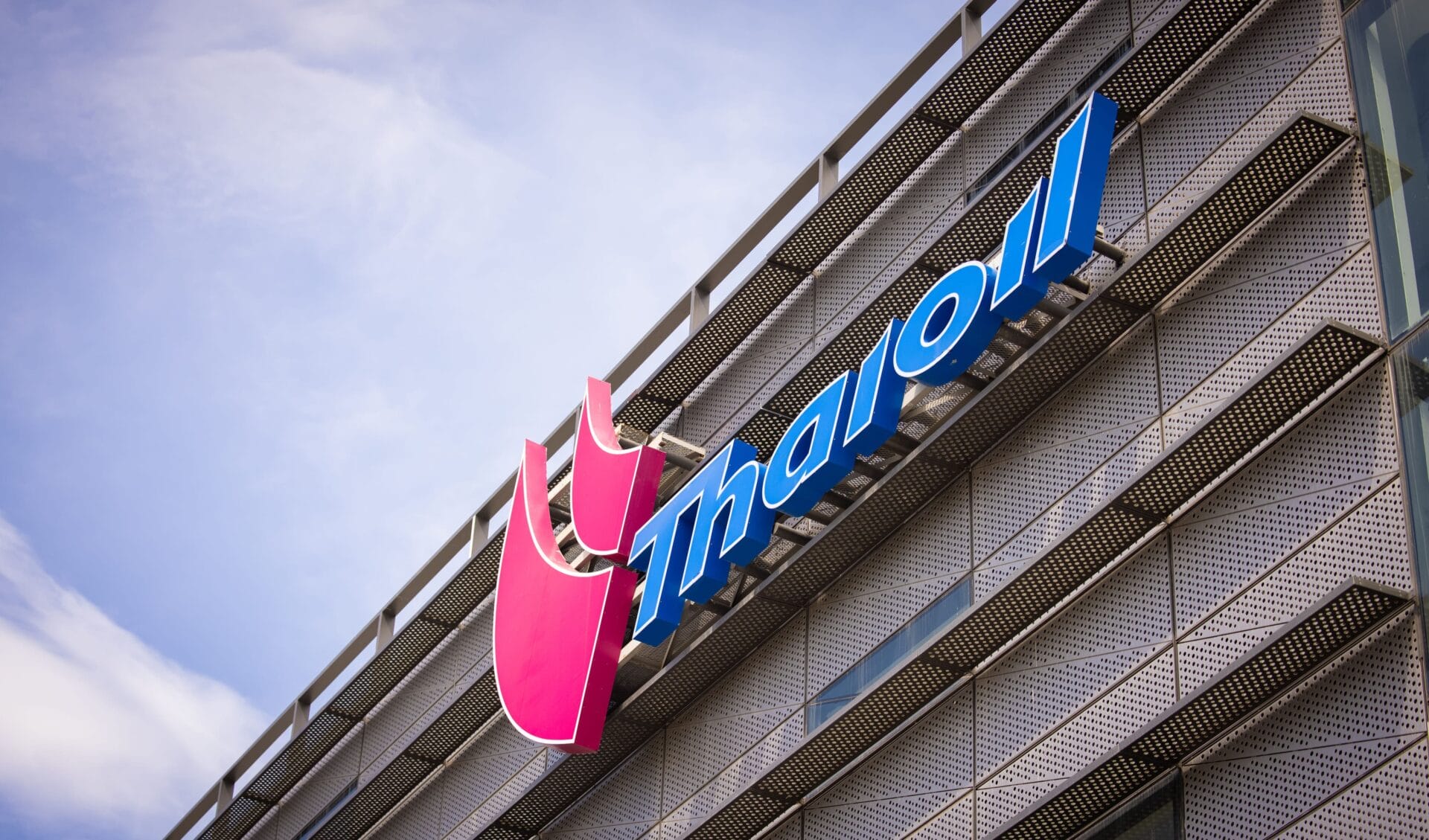
Bangkok
555/1 Energy Complex Building A, 11th Floor Vibhavadi Rangsit Road, Chatuchak, Chatuchak, Bangkok 10900
0 – 2797 – 2999, 0 – 2797 – 2900,
2299 – 0000
Sriracha
42/1 Moo 1, Sukhumvit Road Km. 124, Tungsukla, Sriracha, Chonburi 20230
0 – 3840 – 8500, 0 – 3835 – 9000,
0 – 3849 – 8900
Website
Thai Lube Base Public Company Limited
Our Business
A lube base oil refinery, wholly owned by Thai Oil Plc
Commencement of Commercial Operation
1997
Type of Business
Lube base oil refinery
Capacity
Lube Base Oil
267,015
Bitumen/Asphalt
350,000
Treated Distillate Aromatic Extract
67,520
* Tons per year
Shareholding Structure
Wholly owned by Thai Oil Plc
Products
Vel pretium dolor tellus id purus felis tellus cursus. Amet turpis vel enim aliquet maecenas. Egestas nulla urna suspendisse cursus aliquam mauris facilisis.
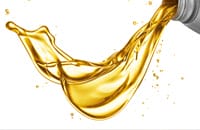
Lube Base Oil
Lube base oil is a product derived from the refining process of crude oil, followed by quality enhancement processes to produce high-purity base oils of various viscosities, such as 150 SN and 500 SN. The higher the number, the greater the viscosity, making it suitable for applications with higher friction.
Thai Lube Base Public Company Limited offers high-quality lube base oil, including:
- 150 SN: Used in the production of industrial lubricants for sectors such as automotive and transportation.
- 500 SN: Utilized in manufacturing automotive engine oils for cars, trucks, and motorcycles.
- 150 BS: Employed in the creation of heavy-duty engine oils for trucks, trains, marine engines, and synthetic industries.
When additives are blended with Thaioil’s lube base oil or lubricating oil (often referred to as “motor oil”), it becomes effective for lubricating various engine components that experience continuous movement, such as the piston shaft. This oil reduces friction and helps cool the engine.
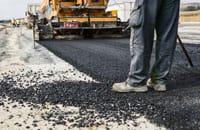
Bitumen (or Asphalt)
Bitumen (or asphalt) is the heaviest product derived from the distillation of crude oil. It is primarily used to create paving materials for surfaces such as roads, parking lots, and airport runways. Bitumen is known for its high viscosity and excellent binding properties; it softens when exposed to heat and hardens as it cools.
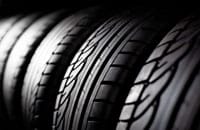
By-products
Aromatic Extract is a by-product obtained through solvent extraction. It is used in the manufacture of SBR (Styrene-Butadiene Rubber), automotive tires, grease, and toner.
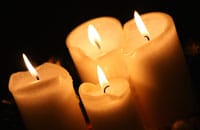
Special products
TDAE (Treated Distillate Aromatics Extract) is produced by reprocessing aromatic extracts to eliminate polycyclic aromatic hydrocarbons and reduce air pollution. It is utilized in the automotive rubber industry.
Slack Wax is a waxy substance used as a raw material in the production of candles, shoe polish, glossing agents, cosmetics, and as a binder in plywood manufacturing.
Lube Base Oil Refinery Production Processes
The products of TLB’s processes are lube base oil of three distinct grades grouped by viscosity, namely 150 SN, 500 SN, and 150 BS, bitumen/asphalt, aromatic extracts, TDAE, VGO, slack wax, and naphtha.
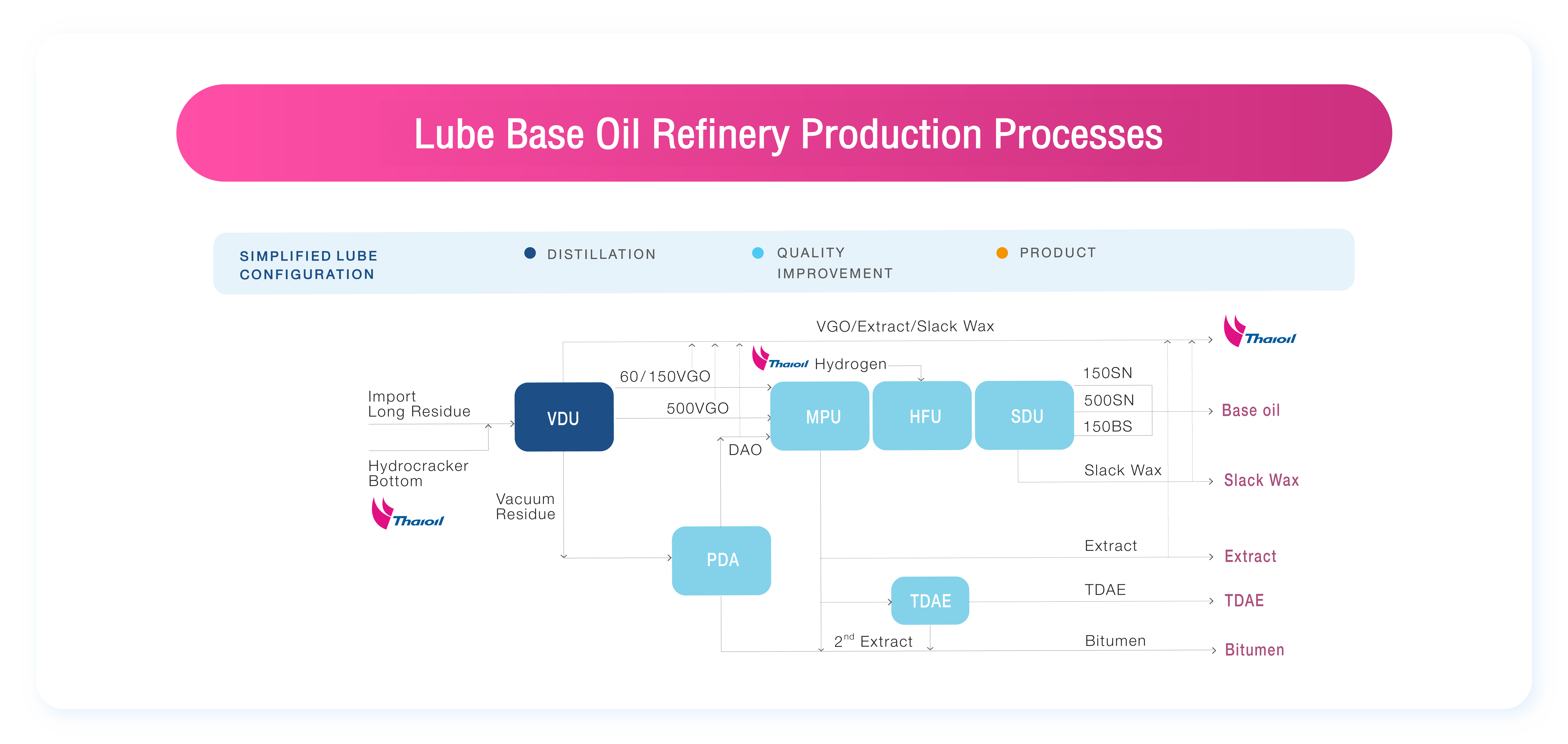
Lube Base Oil Refinery Production Processes
The Vacuum Distillation Unit is the first step in the production process, responsible for distilling and separating oil grades at different temperatures under vacuum pressure. This unit produces three grades of Vacuum Gas Oil (VGO), which are used as feedstock for the further production of base oils.
The Propane Deasphalting Unit operates by extracting asphalt from the vacuum residue at the bottom of the vacuum distillation tower, utilizing propane as a solvent. This process yields Deasphalted Oil, which serves as a raw material for producing 150 Bright Stock (150BS) base oil, as well as asphalt, which is used as feedstock for further bitumen production.
The MP Refining Unit extracts aromatics from Vacuum Gas Oil (VGO) and Deasphalted Oil using N-Methyl-2-pyrrolidone (NMP) as a solvent. This process produces raffinates with a higher viscosity index.
The Hydrofinishing Unit is responsible for removing sulfur from the raffinates through a hydrogenation reaction, resulting in hydrotreated raffinates that are purer and clearer.
The Solvent Dewaxing Unit separates Slack Wax from Hydrotreated Raffinates, producing base oil products with low pour points that meet international standards and are ready for sale.
The Treated Distillate Aromatic Extract (TDAE) Unit separates polycyclic aromatics to produce a low-toxicity rubber processing oil known as TDAE.
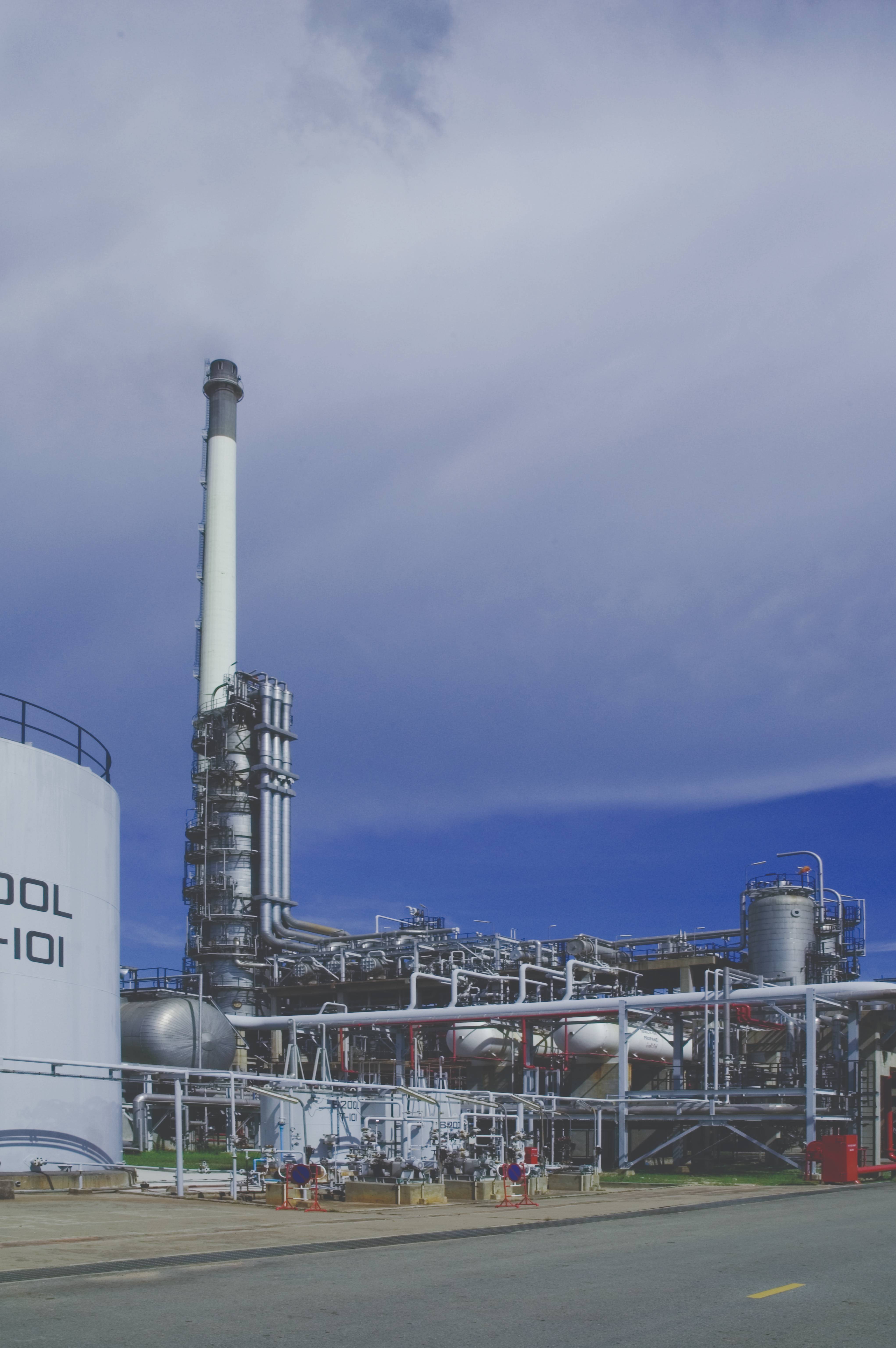
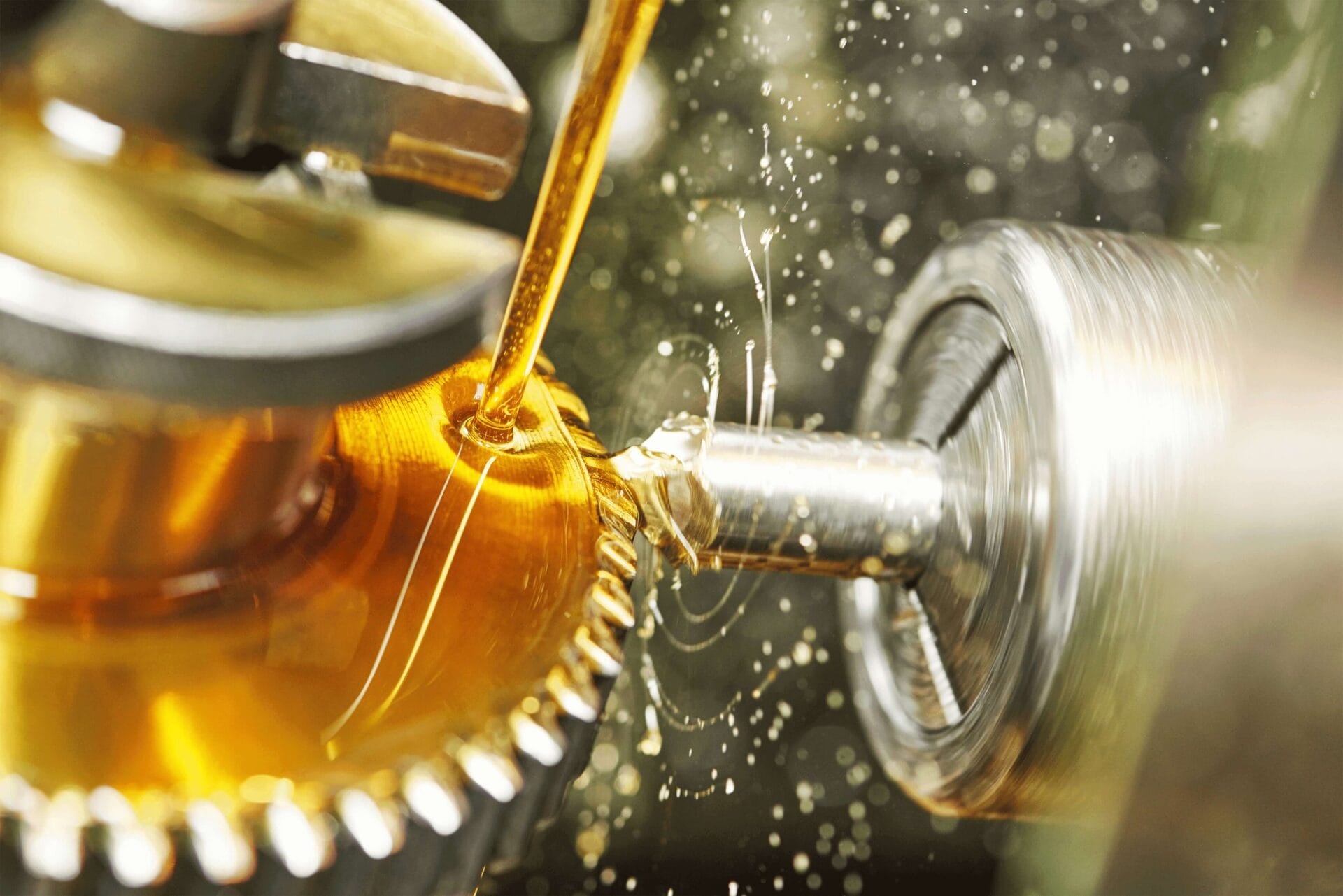
General Information
Vel pretium dolor tellus id purus felis tellus cursus. Amet turpis vel enim aliquet maecenas. Egestas nulla urna suspendisse cursus aliquam mauris facilisis.Vel pretium dolor tellus id purus felis tellus cursus.
Acronym
TLB
Registration Number
0107539000090
Business Type
Lube base oil refinery
Registered Capital (Baht)
1,757,890,730 Baht
Type of Share
Common
Number of Share
(Sold)
175,789,073
Value of Share (Baht/Share)
10 Baht

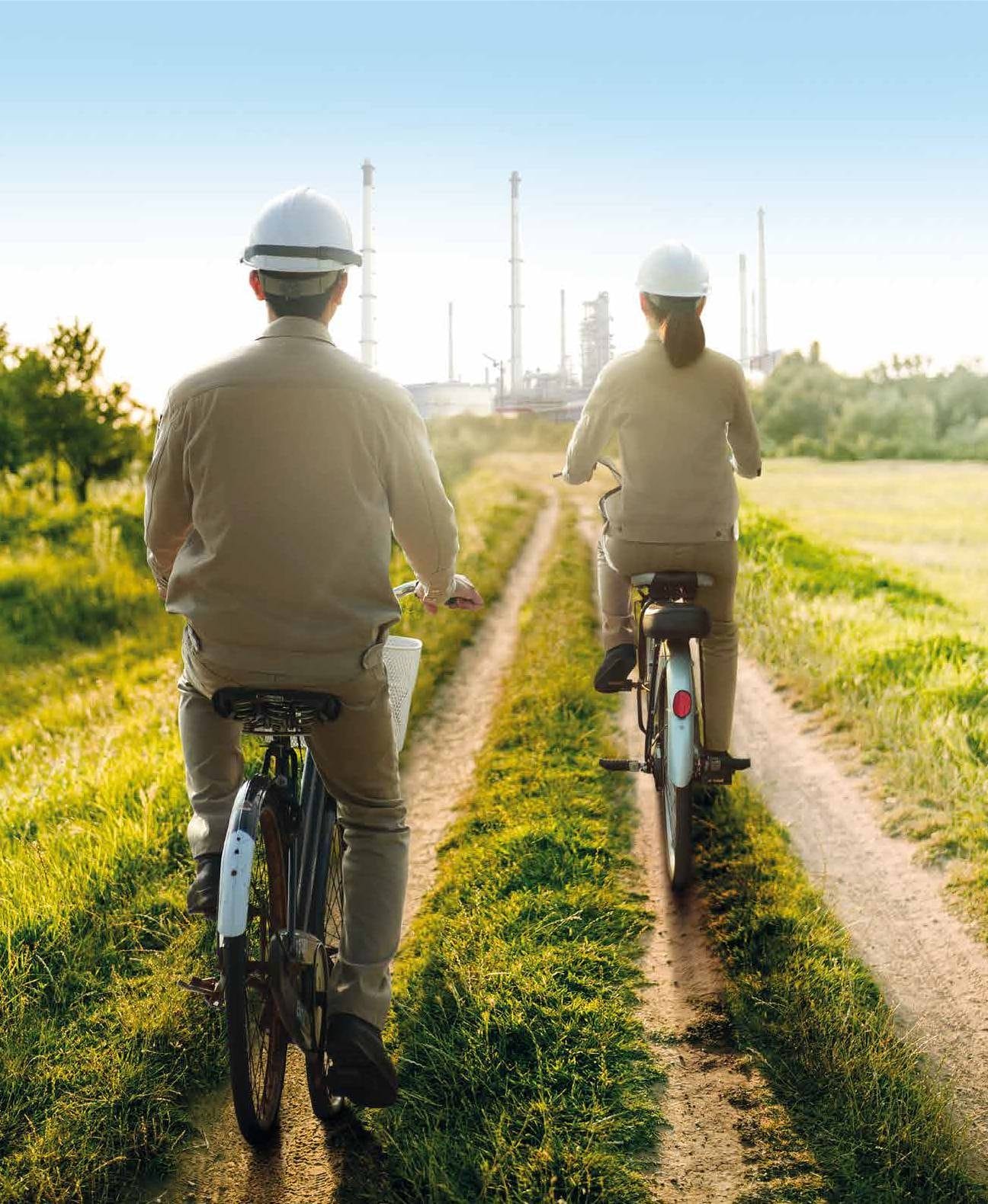
Contact Us
Thai Lube Base Public Company Limited
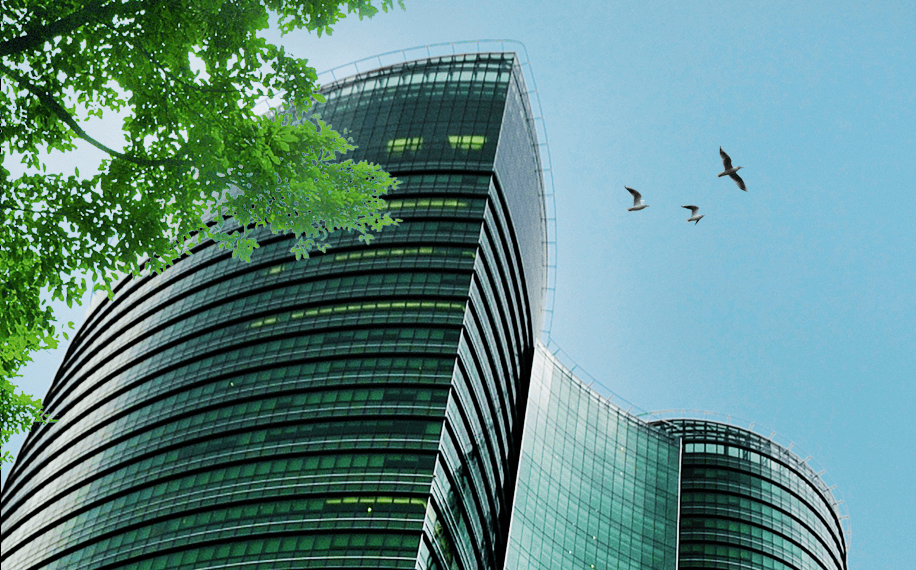