Environmental
Impact Management
Challenges, Risks,
and Impacts
ensuring strict compliance with environmental regulations, promoting a circular economy, preparing for potential drought situations, and safeguarding biodiversity. In addition to these challenges, Thaioil Group recognizes the impact of the business operations on local communities, which requires effective management to mitigate associated risks. Consequently, Thaioil Group enhanced its management approach in construction projects and implemented controls over the production process to prevent adverse effects on the community’s lifestyle and well-being. To achieve this, the company has integrated the sustainability or Environment, Social, and Governance (ESG) management process into its operations to enhance work processes and procedures, thereby reducing environmental impacts on communities and other stakeholders. This approach is applied to all sizes of Thaioil Group’s construction projects. Likewise, the Company maintains strict control over the current production process to ensure normal operating conditions. Moreover, Thaioil Group consistently places significant emphasis on regulatory compliance inspections and preparpadness for emergencies that may arise and impact the environment.
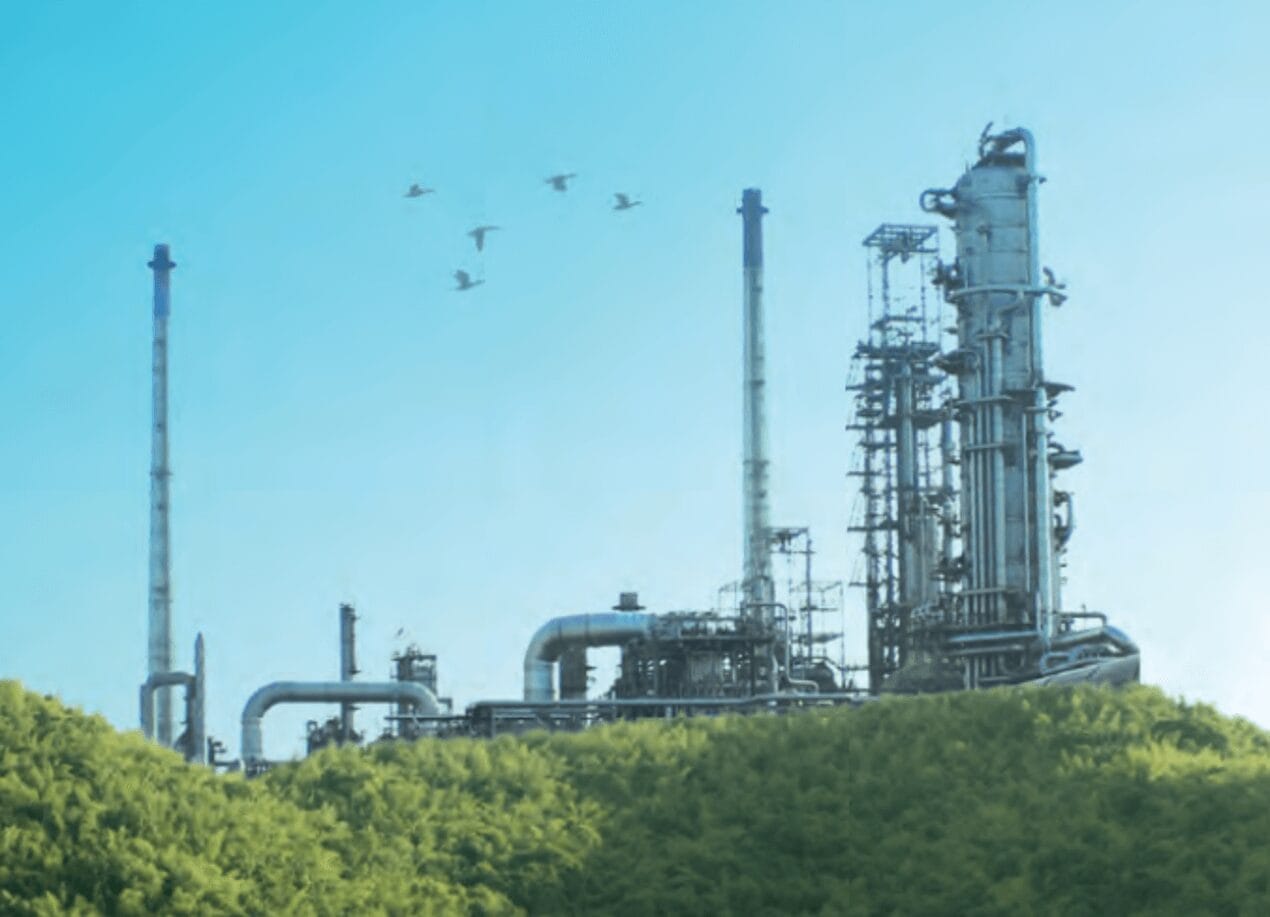
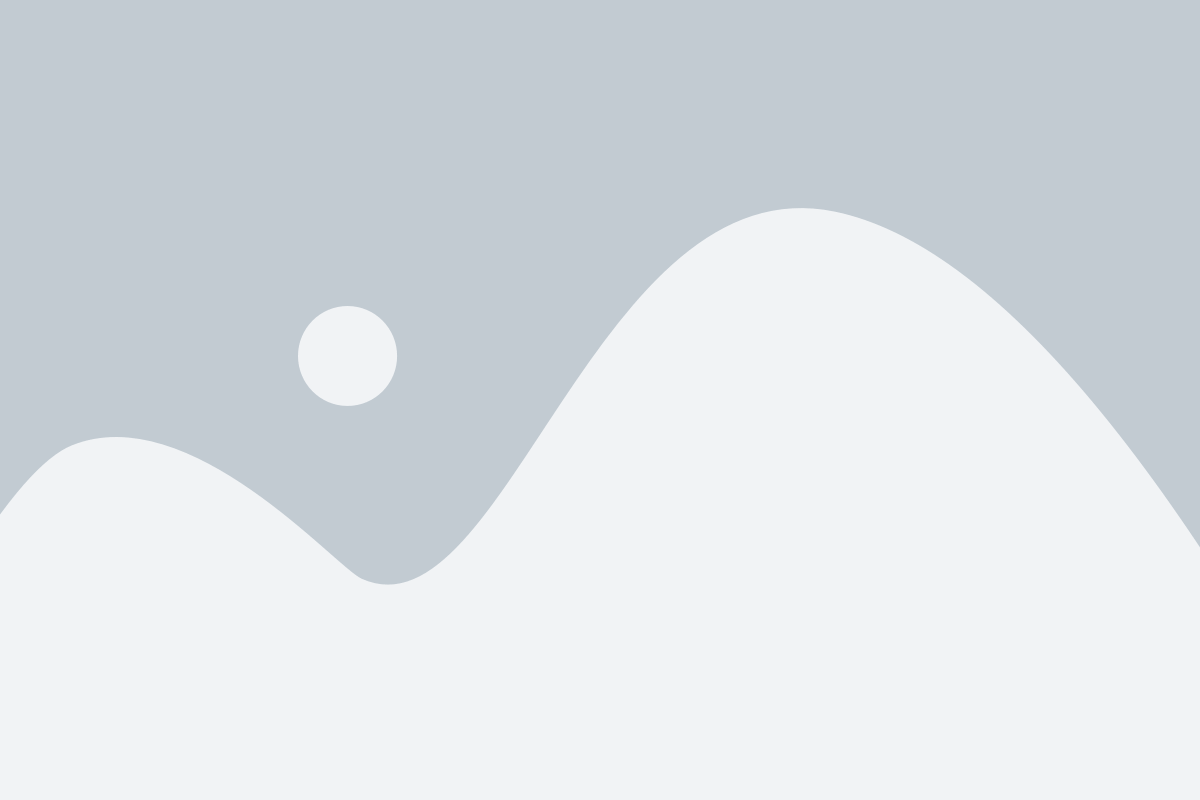
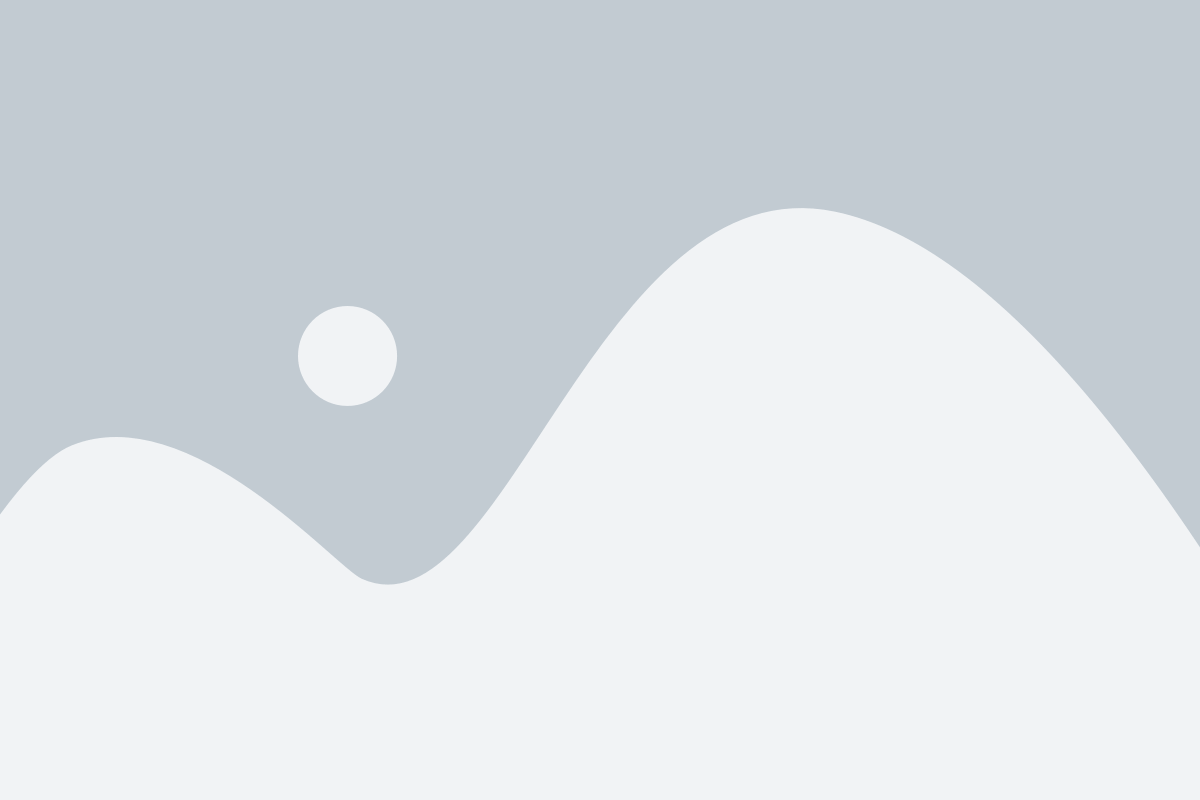
Thaioil Group strives to enhance the Company’s environmental management system in alignment with global trends, aiming to drive towards sustainable business growth while maintaining environmental awareness. According to the Environment, Social, and Governance (ESG) practices, the Company aims to reduce environmental impacts and create long-term business opportunities in collaboration with the community as specified in the policy.
In addition, the Company has adopted an environmental management system in accordance with national and international standards to oversee and continually improve the management system and environmental master plan. In 2023, Thaioil Group elevated the policy commitment in Thaioil and Subsidiaries’ Quality, Security, Safety, Occupational Health, Environment, and Energy Management Policy through the approval of the Board of Directors to consistently drive the most efficient environmental management practices.
Targets
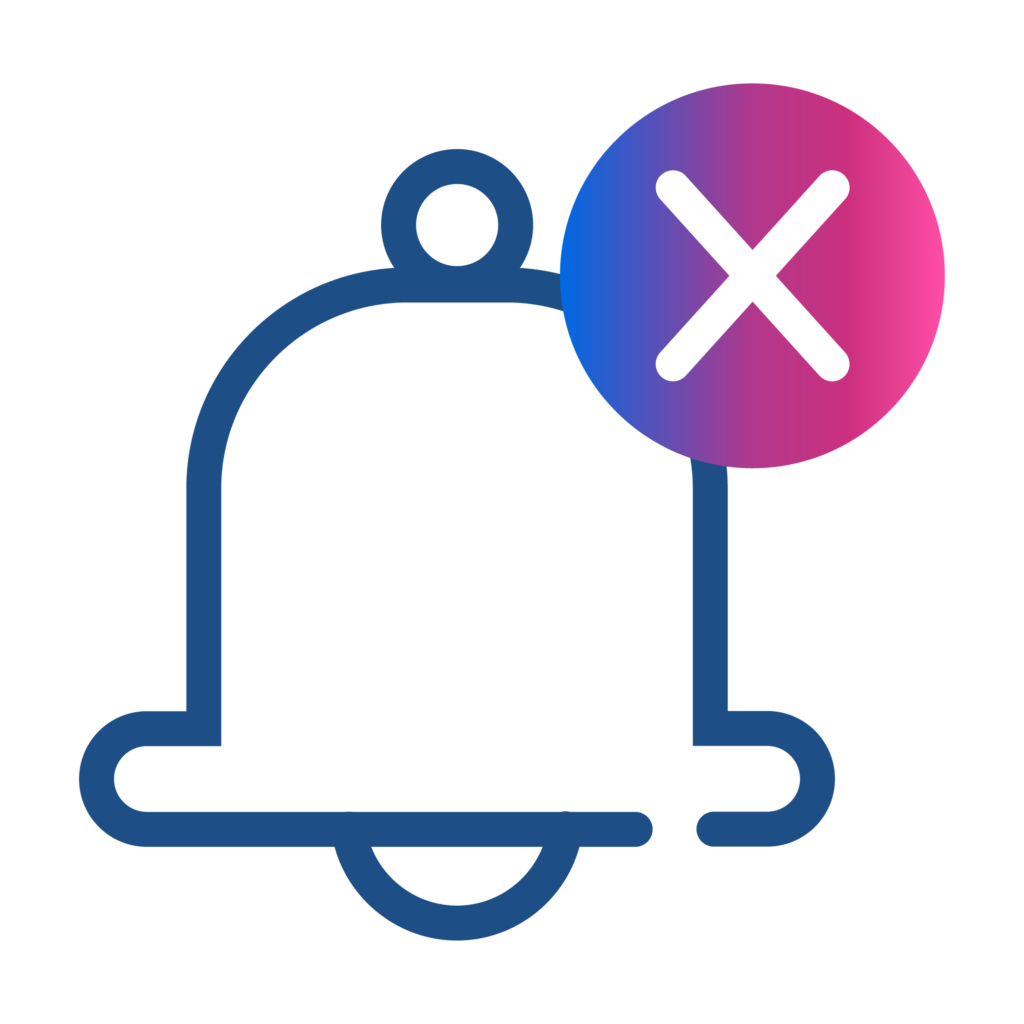
Complaints on environmental incidents
Targets 2024
0
Case
Long-term targets 2030
0
Case
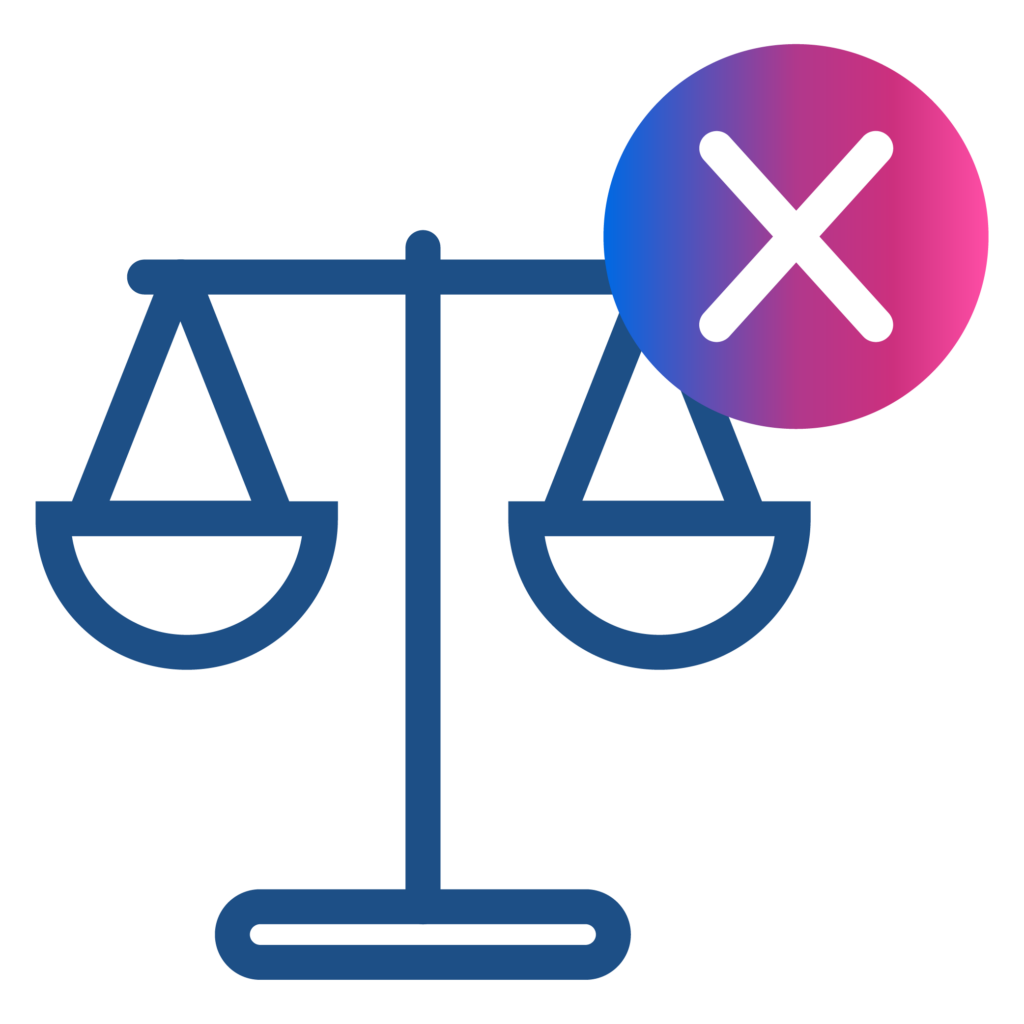
Non-compliance with relevant environmental laws and regulations
Targets 2024
0
Case
Long-term targets 2030
0
Case
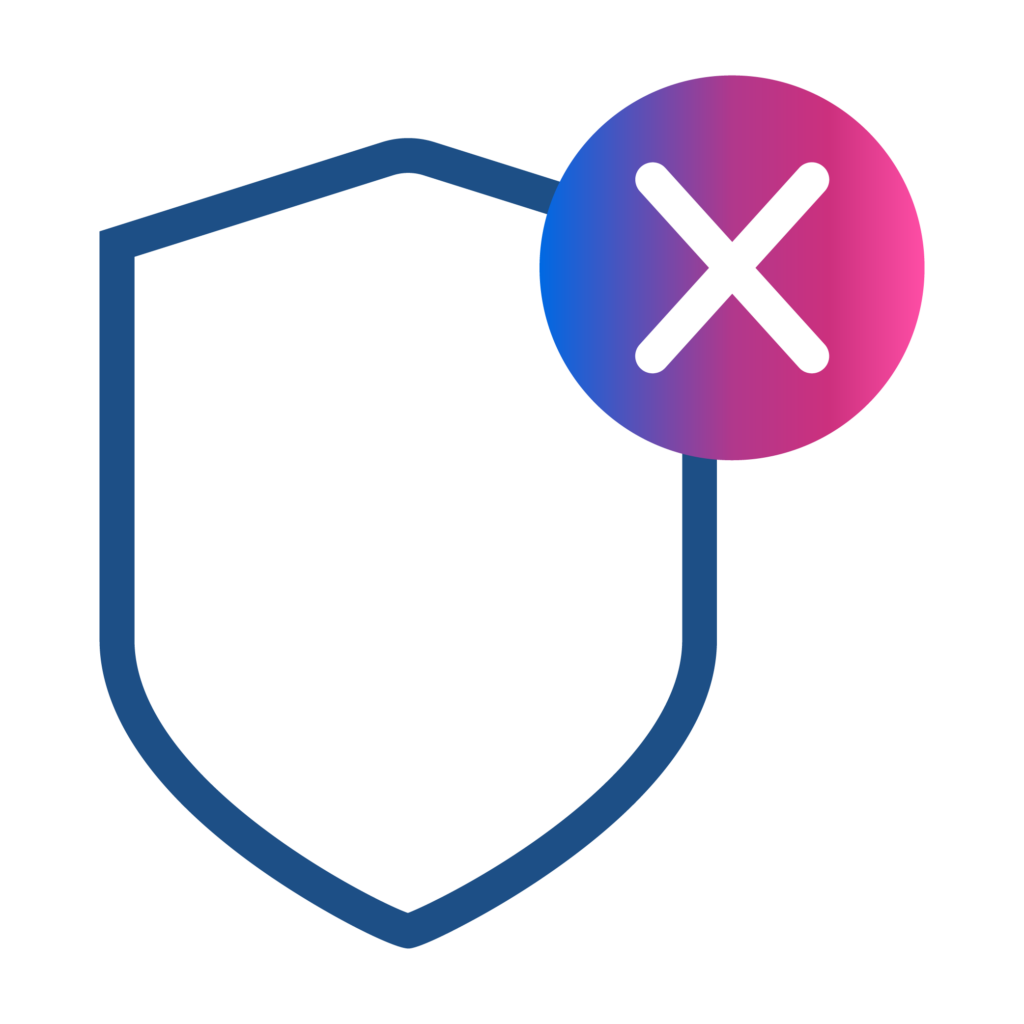
Major non-compliance with ISO 14001: 2015 standard
Targets 2024
0
Case
Long-term targets 2030
0
Case
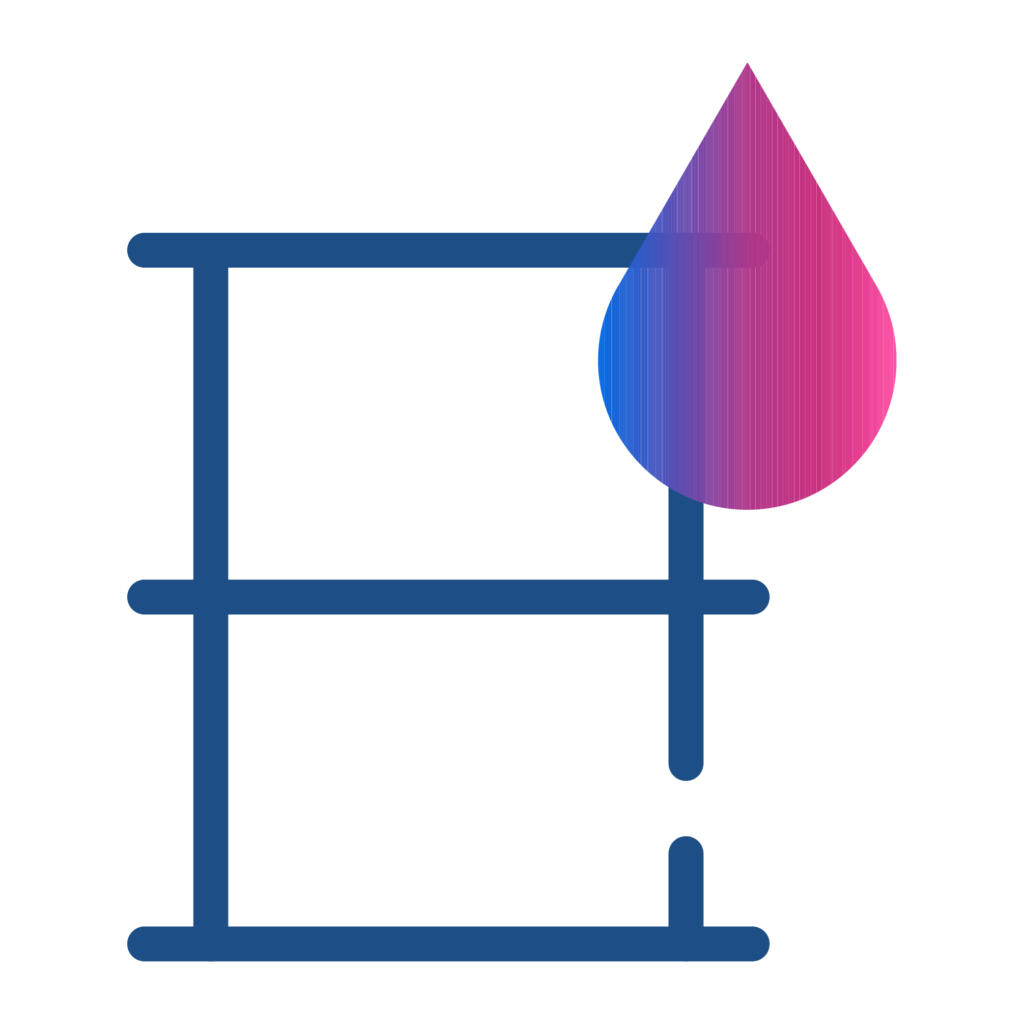
Significant oil and chemical spills into the environment
Targets 2024
0
Case of significant spill
Long-term targets 2030
0
Case of significant spill
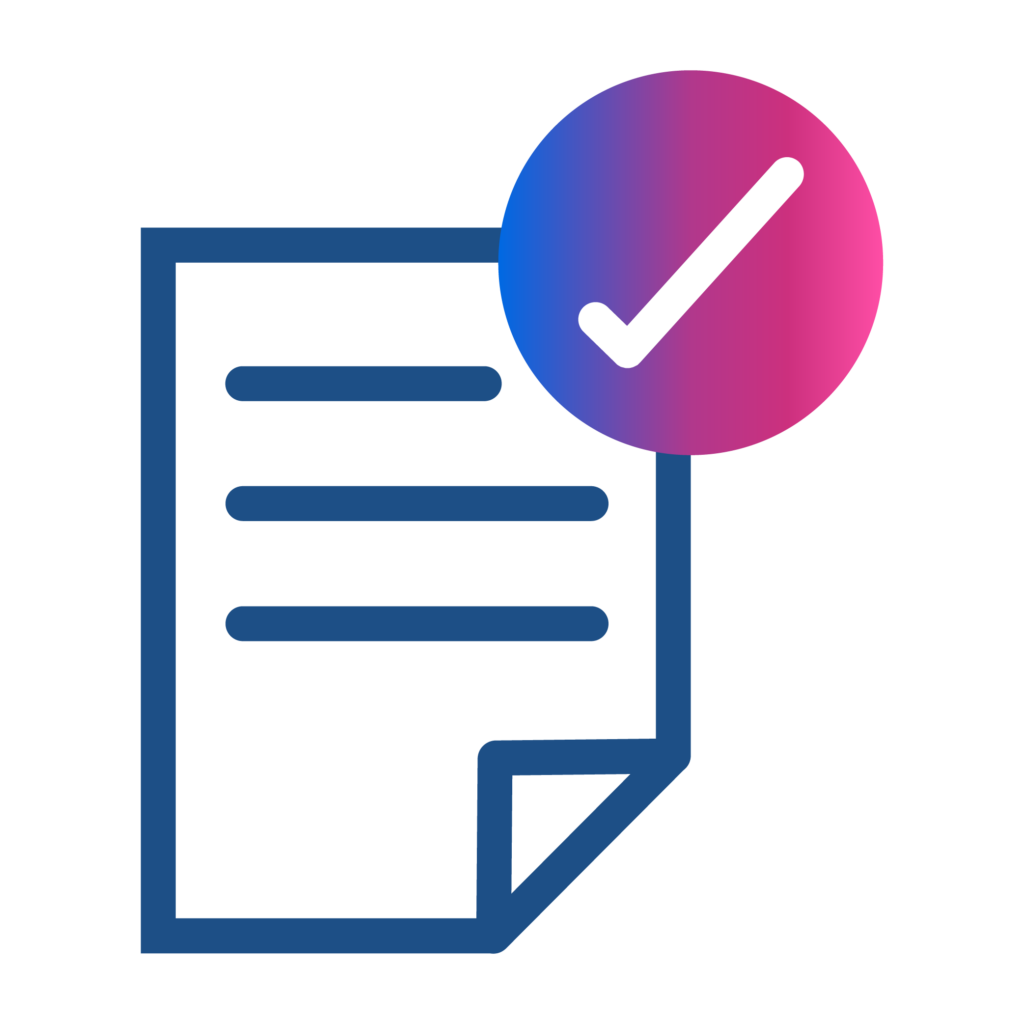
Compliance with excellent environmental governance standards in petroleum and petrochemical refineries
Targets 2024
100
Percentage
Long-term targets 2030
100
Percentage
Management Approach
and Performance
Environmental Management
Thaioil has defined the roles and responsibilities for implementing Quality, Security, Safety, Health, Environment, Energy Management (QSHE policy), with the goal of efficient resource management and continuous improvement. The Roles and Responsibilities extend to executives and employees at all level, including
(1) Chief Executive Officer and President
- Determine roles, responsibilities, and duties of all operation levels throughout the organization in relation to the Company environmental management system.
- Appoint an acting representative(s) according to appropriate chain of command and communicate this appointment to relevant employees and entities to ensure that operations adhere to Continuous Management System requirements.
- Ensure that all management system manuals and work procedures are properly documented and communicated to employees. This can be achieved through lines of supervisors and training. In this case, once this is done, the documents much be stored in the central database of Thaioil Group, where they can be easily accessed by all employees.
- Appoint Manager of Quality System to be a representative for QSHE Management Representative (QSHE-MR) according to the organizational structure and responsible for:
- Develop, utilize and maintain management system and document.
- Encourage all relevant personnel to be aware of the needs and expectations of all stakeholders. This includes understanding and complying with all legal and other requirements related to the QSHE management system.
- Report on the performance of QSHE management system to management team for review and recommendation for improvement.
(2) All management levels and Department managers
- Clearly identify the roles and responsibilities of those involved in QSHE management system to ensure that processes meet objectives and targets and respond to needs and expectations of all stakeholders.
- Sufficiently allocate resources, such as human capital, skills, facilities and technology, to prepare and maintain the management system.
- Provide clear directions and communicate to employees and contractors at all levels to understand and strictly adhere to the QSHE policy.
(3) Employees and contractors
- Employees and contractors at all levels comprehend and strictly comply with the QSHE policy in order to efficiently achieve the goals and objectives.
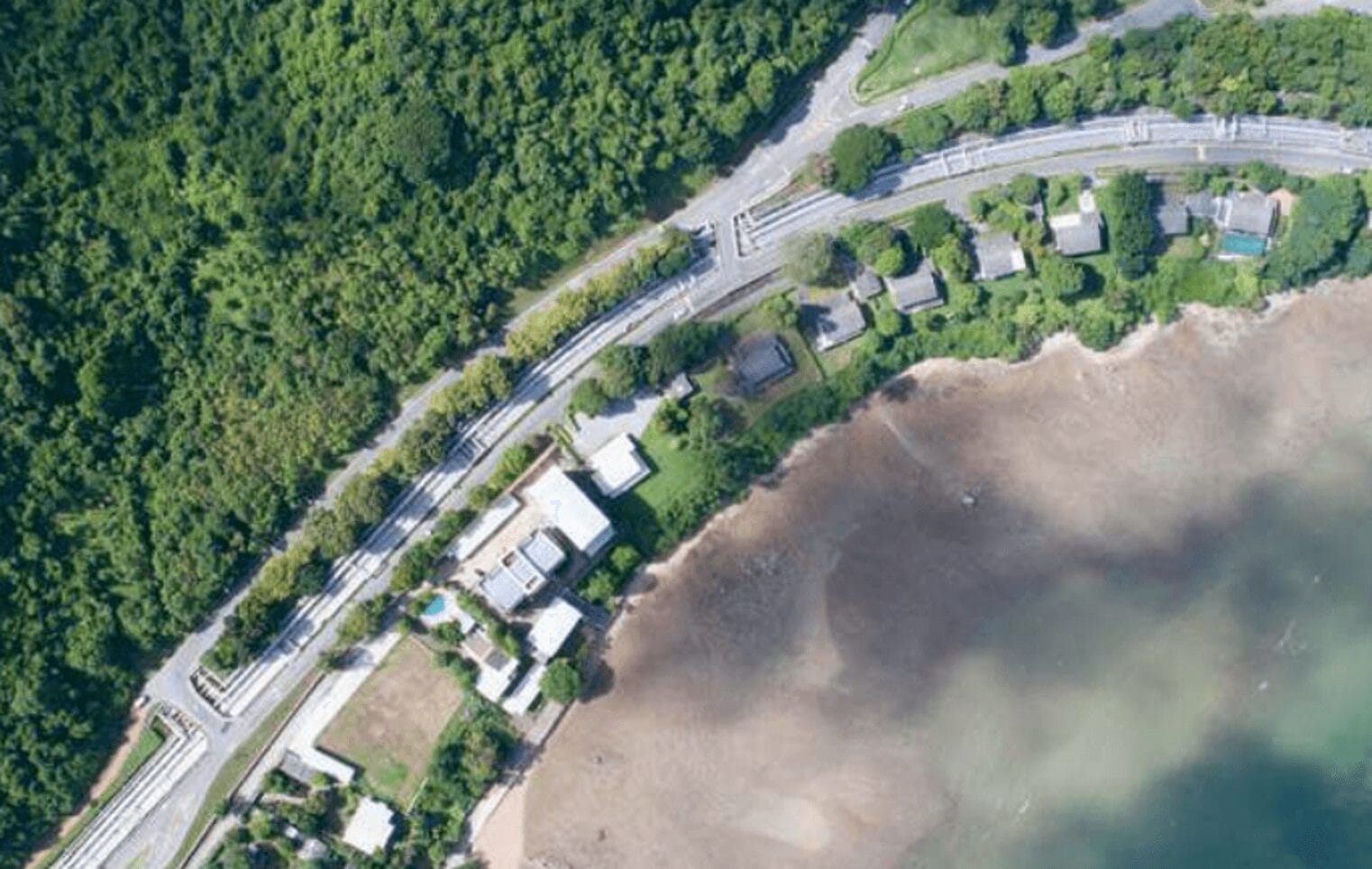
Management Approach
Thaioil Group is committed to fulfilling its responsibilities across three key areas, namely Environment, Social, and Governance (ESG). The Company has adopted the principles of a circular economy to drive business growth. A comprehensive environmental strategy and master plan have been developed to guide short, medium, and long-term initiatives, ensuring environmentally conscious operations and minimizing environmental impacts throughout the production chain towards sustainable business growth.
Long-term Strategy
Thaioil Group is committed to promoting business growth while maintaining environmental consciousness and creating long-term business opportunities. This commitment comprises two key strategies, namely the Net Zero GHG Emissions strategy and the Circular Economy strategy, both of which are supported by a well-defined governance structure.
Short to Medium-term Strategy
Thaioil Group is committed to minimizing environmental impacts at their sources and promoting ESG practices that are resilient to changes and aligned with global trends and the long-term business strategy. The Company has aligned the strategic management plan towards O2Bx (Operation Excellence to Business Excellence). In addition, the “Refinery in The City” model has been adopted in the management approach in pursuit of business excellence, focusing on three main areas on environmental management, social management, and governance compliance. To efficiently achieve these business excellences, Thaioil Group has implemented a management approach known as the “CARE Concept”, which is outlined as
CARE Concept
C
C – Control Right
Controlling environmental impacts and maintaining compliance with the regulatory requirements. The environmental management has been elevated through Permit to Work-Job Safety Environmental Analysis (JSEA) to prevent and minimize potential impacts on communities that may be affected by the Company’s production, construction, and transportation activities. The Company has also proactively prepared to mitigate impacts from the Clean Fuel Project (CFP), which is in the process of commissioning and start-up. This aims to maintain the trust of the surrounding community through active community engagement.
A
A – Awareness & Communication Right:
Raising awareness, engaging in communication with stakeholders, and building trust in Thaioil Group’s ability to prevent and mitigate the impacts of business operations. This is outlined in the Company’s Sustainability Management Policy and Corporate Social Responsibility Policy. This aims to enhance the quality of life for communities and society, contributing to sustainable growth.
R
R – Recycling Right
Managing natural resources efficiency through the 3Rs strategy (Reduce, Reuse, Recycle) and the circular economy principle, in order to support the Sustainable Development Goals such as TOP CE WE GO (Waste to Products) and CE for Community projects.
E
E – Eco-Society Right
Creating value to society through the “Partner for Life CSR” concept to instill volunteerism and corporate social responsibility among employees. Furthermore, the Company promotes a “Volunteer Culture” and encourages employees to design initiatives for communities towards “Share Value with Society”.
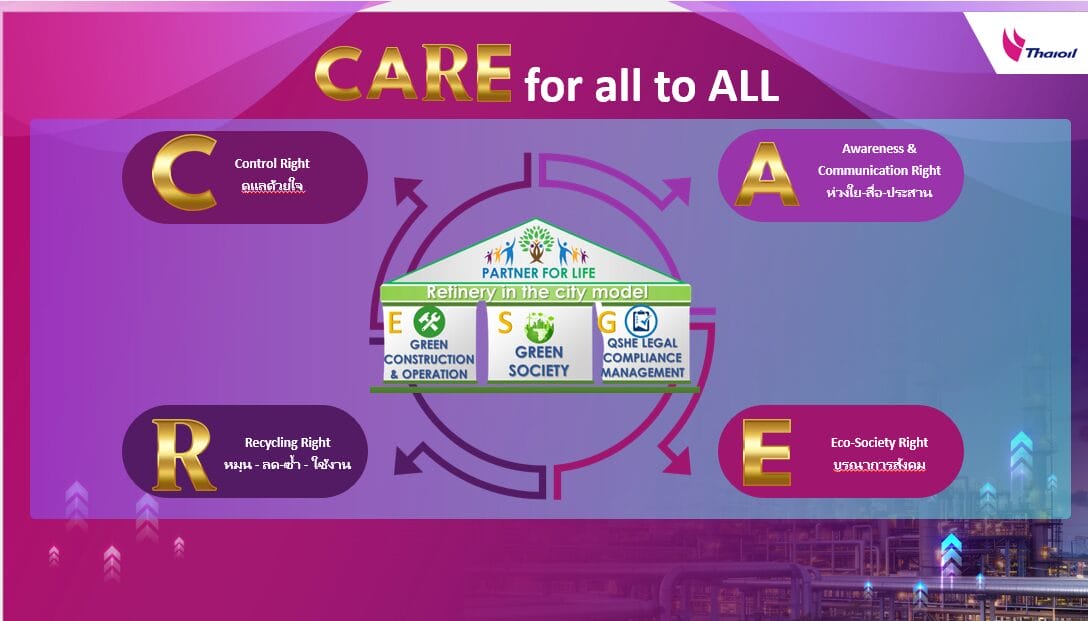
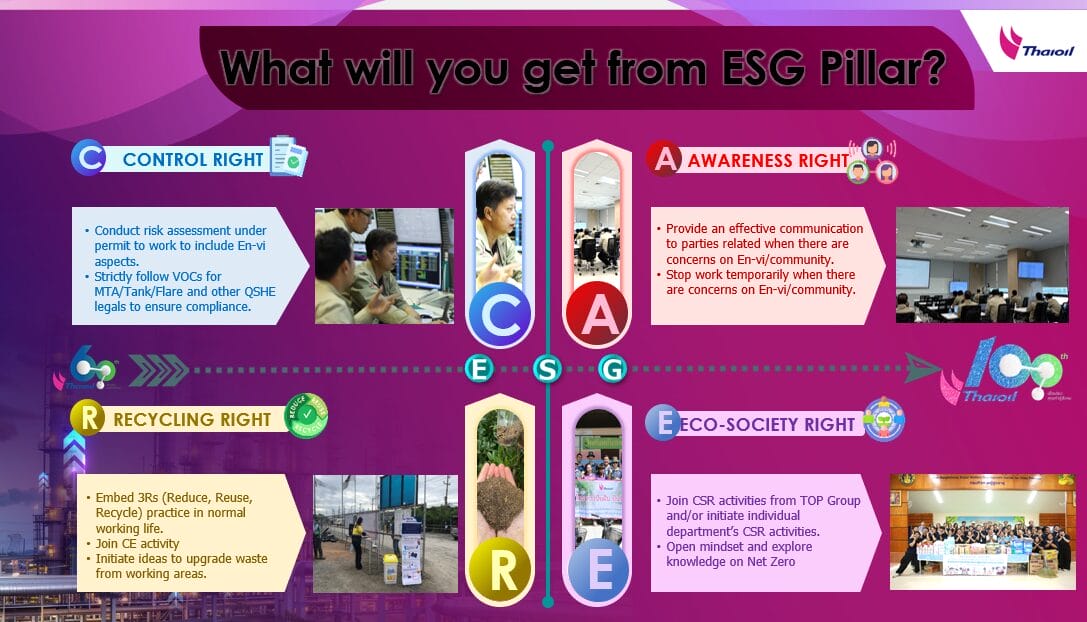
Becoming The Partner
For Life Through
A Trusted Partner for Life
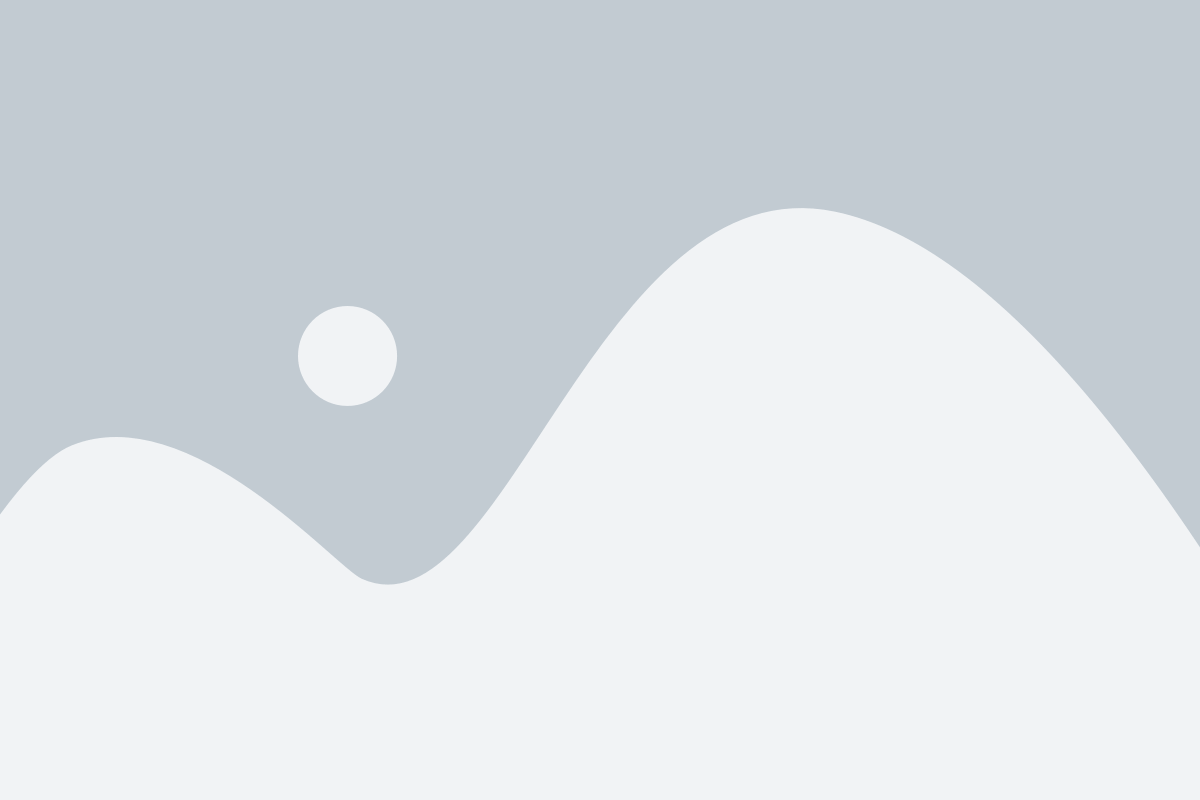
Thaioil Group operates business with transparency and fairness, prioritizing the appropriate return of benefits to all groups of stakeholders as well as emphasizing environmental protection and community well-being. To achieve this goal, the Company implements a comprehensive environmental management plan that considers both internal and external environmental factors (Environmental Outlook) to align with the needs and expectations of the stakeholders. This involves communities, government agencies, executives, and employees who have expertise in environmental topics, as well as environmental regulations, laws, and global megatrends, etc. All factors are analyzed to identify business opportunities and enhance a five-year environmental plan referred to as the “5 Years Environmental Master Plan”. This plan is used as the key framework to drive sustainability in environmental management and ensure effective environmental management to achieve the environmental targets.
Thaioil Group enhances employees’ knowledge on environmental management in alignment with the sustainability and environmental policies and practices. For instance, the Company organized training sessions on carbon taxes, Net Zero GHG Emissions, Carbon Footprint Organization and Carbon Footprint Products. In addition, statutory training was also conducted for environmental managers and practitioners in pollution treatment systems, which was attended by 113 attendants. The Company is committed to providing training on an annual basis to enhance employees’ knowledge of environmental management for continuous efficiency.
Furthermore, Thaioil Group governs and develops environmental management systems according to accepted standards at the national and international levels. For example, ISO 14001 (the standard on environmental management excellence) and evidence of the Company’s environmental management system (EMS) audits (ISO 14001) for all operating locations is available on the Company’s website https://www.thaioilgroup.com/en/about/management-system/, ISO 26000 (the standard on corporate social responsibility) under the CSR-DIW project, PTT Group’s Operational Excellence Management System (OEMS), the best practices in biodiversity management, the Global Reporting Initiative (GRI), and the best practices identified from the Dow Jones Sustainability Indices (DJSI) assessment. To improve and develop environmental management systems, these standards are adopted in risk assessments, environmental prevention and mitigation measures, operational controls, monitoring, inspection, and reporting processes, as well as the execution of the proactive and reactive environmental indicators. The Company has also improved and developed the environmental management system throughout the production process to end products across the value chain, covering operations in various conditions as follows:
Thaioil Group reviews risks, environmental issues, and preventive measures to mitigate environmental impacts at the sources on an annual basis or when significant changes occur. Moreover, the Company has been steadily enhancing production efficiency in accordance with the Environmental Master Plan, which serves as the operational framework and comprises the following topics:
- Governance
- Environmental Technical Procedures
- Climate Strategy
- Water Resource Management
- Eco-efficiency
- Biodiversity
- Supplier and Contractor Program
- Environmental Audit
- Management Information Solutions
For the refinery unit expansion project, Thaioil Group applies the environmental standard specifications, which encompasses the requirements, laws, best practices, and fair stakeholder perspectives, based on the environmental principles. This aims to establish the operating framework for the Green Construction Project. The framework remains continuously responsive to the requirements and expectations of relevant stakeholders.
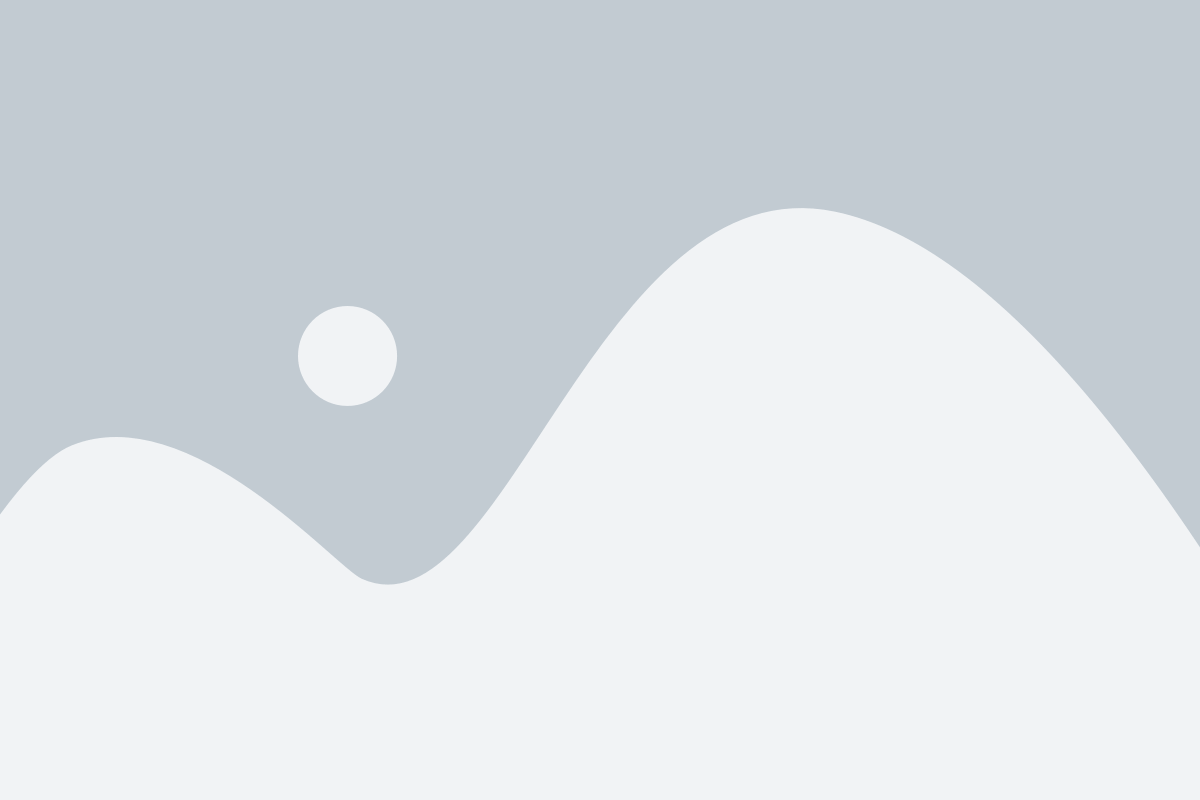
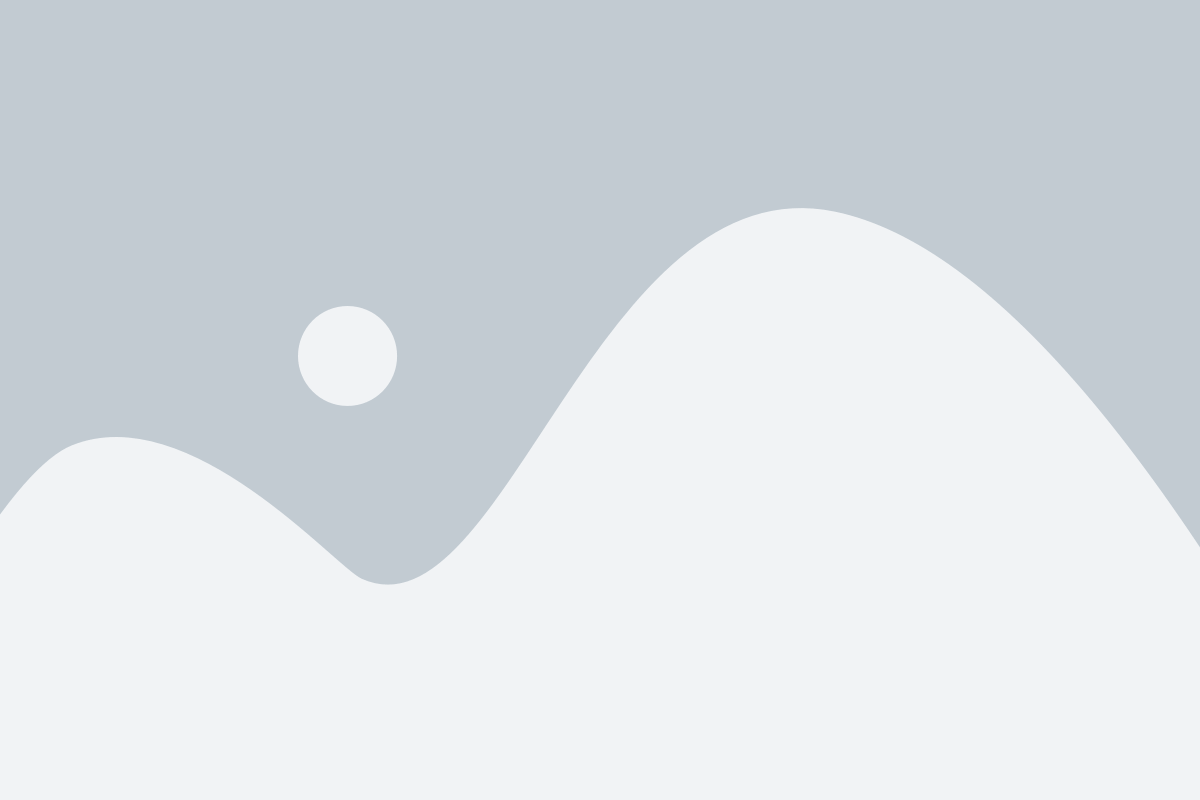
Key Highlighted Projects
In 2024, Thaioil Group implemented additional projects as follows:
The best practice principle has been applied to reduce emissions and minimize the loss of volatile organic compounds (VOCs)
Thaioil Group has established the Environment and Community Relation Committee (ECRC). The Company has worked in partnership with the government agencies, academies, and communities surrounding the production area to improve environmental management and mitigate impacts on all stakeholders. The Company has adopted a collaborative approach, adhering to the “3-synchronization model” and the “5-Together” conceptual framework, fostering a collaborative approach that emphasises joint efforts in thinking, working, correcting, learning, and developing together. This collaboration starts with establishing proactive guidelines and working together to resolve issues during abnormal operating conditions. Environmental performance is monitored and assessed 24 hours a day, seven days a week by the operational team. Furthermore, the ECRC also organizes activities and communication platforms to track and monitor environmental performance in compliance with the requirements, regulations, and operating targets. To ensure the least environmental impact on the surrounding communities, the ECRC organizes monthly meetings to address concerns and suggestions for further improvement. Additionally, an annual perception survey is conducted with the community.
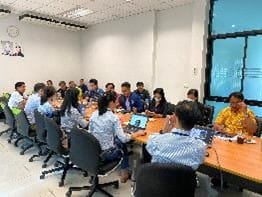
Meeting for the preparation of monitoring and recovery plan with government agencies
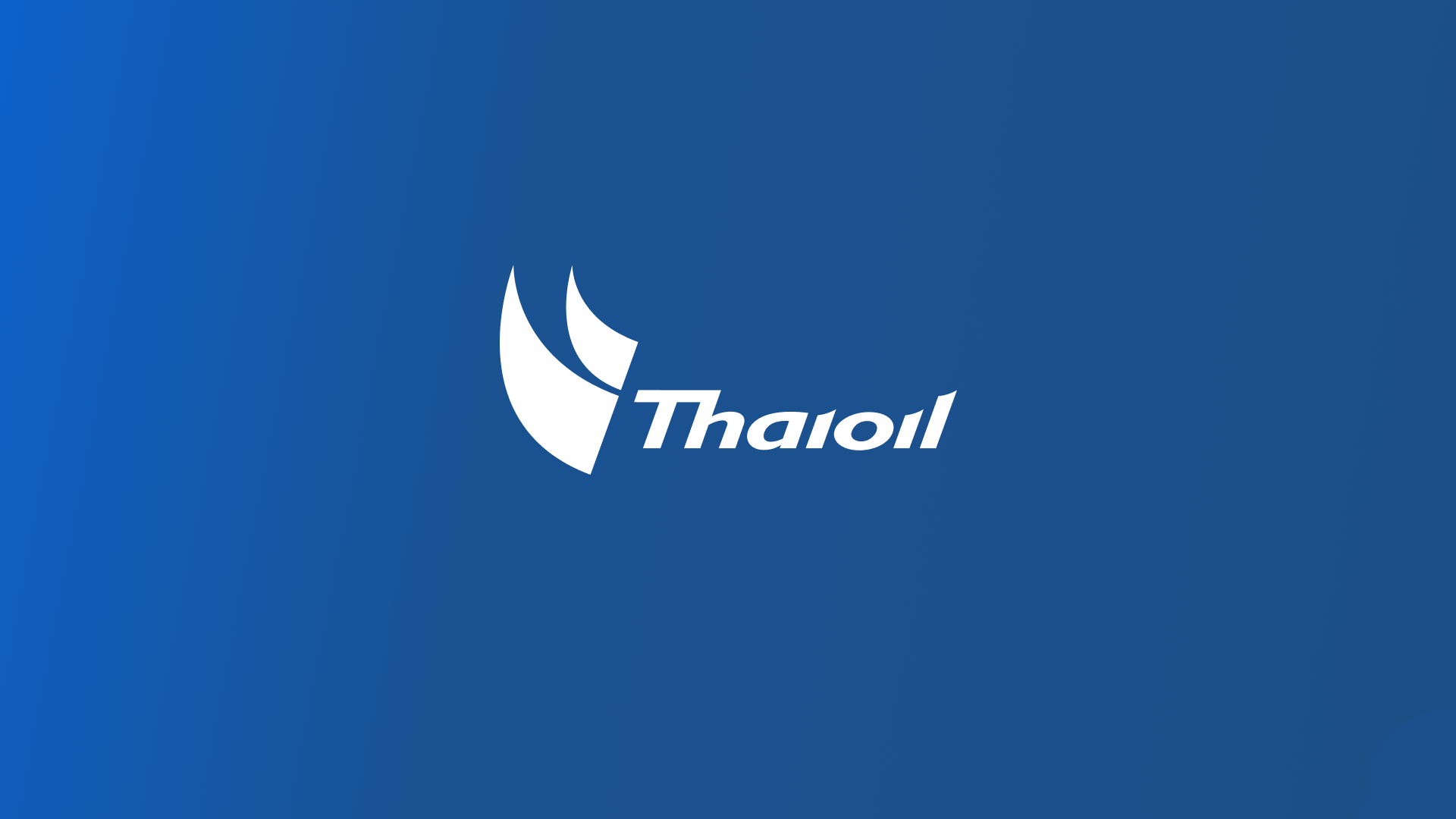

Environmental
Emergency Conditions
The prevention of oil and chemical spills is a critical priority for Thaioil Group’s business operations. In 2024, Thaioil Group reported no case of significant oil and chemical spill in accordance with the criteria of the Oil Industry Environmental Safety Group Association (IESG). The Company has implemented the management approaches in three aspects to efficiently manage the oil and chemical spill as follows:
Utilizing ships that have passed the safety standard assessment of the PTT Group Ship Vetting System.
In this assessment, Captains from the Company and the PTT Group will assess safety documents, including the Ship Inspection Report Programme (SIRE), an international standard of the Oil Companies International Marine Forum (OCIMF), ship information from international websites, such as Sea Website and terminal feedback of the ships shared with the PTT Group. These documents will be reviewed and considered together with the ship quality audit assessment within the PTT Group to ensure the quality of the ships and crew members used by Thaioil Group aligns with international safety standards.
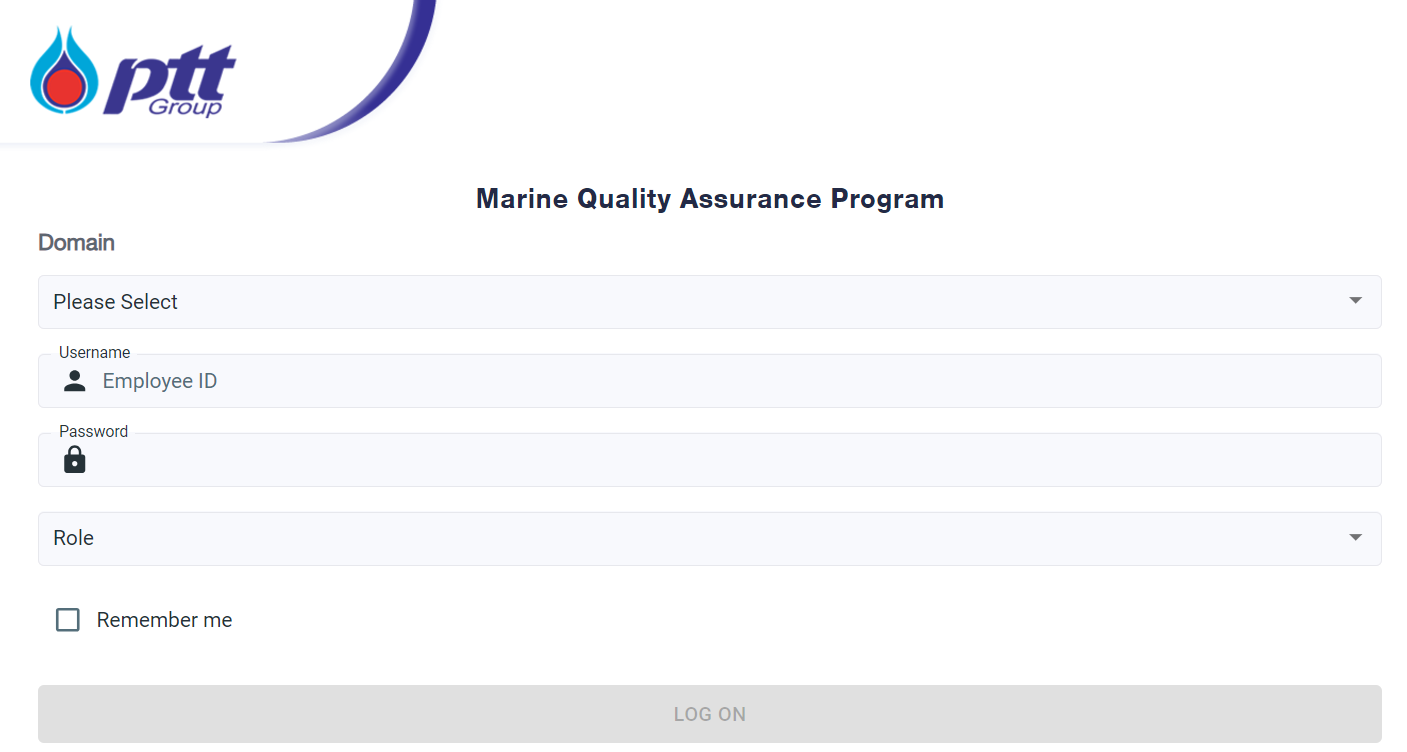
Conducting the Loading master course – Ship Shore Safety Checklist training for employees assigned as Loading masters.
This training aims to provide the necessary knowledge and ensure a understanding of their responsibilities, in accordance with the international standard Marine Terminal Operator Competence and Training Guide (MTOCT).
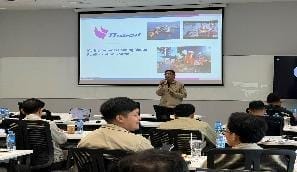
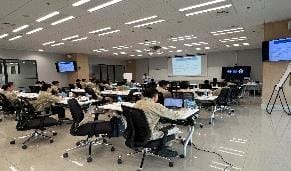
Maintaining and inspecting ports, buoys, and other equipment used for transferring crude oil and petroleum products periodically.
This includes inspections of pipelines at the port and offshore buoys, safety joints, and ship ropes. In 2024, Thaioil Group’s Engineering Department conducted scheduled inspections in compliance with international standards, Single Buoy Mooring Maintenance and Operation Guide (SMOG). Specifically, the inspections included annual inspections, inspections of floating and submarine flexible hoses, and inspections of the Single Buoy Mooring (SBM) in both the SBM-1 and SBM-2. All systems were found to be in compliance with international safety standards. The details of inspections are as follows:
1. Conducting inspections of surface buoys annually with the following procedures:
- Performing visual inspection
- Measuring the thickness of buoys using ultrasonic testing
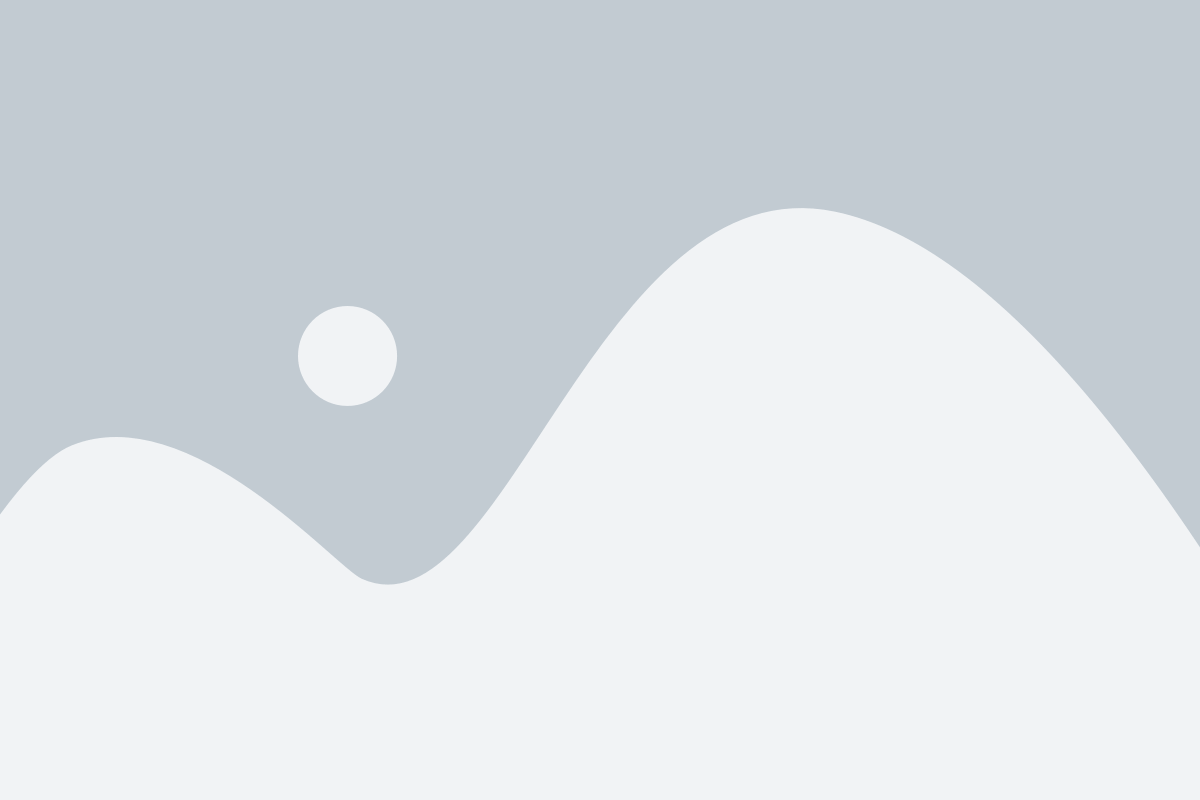
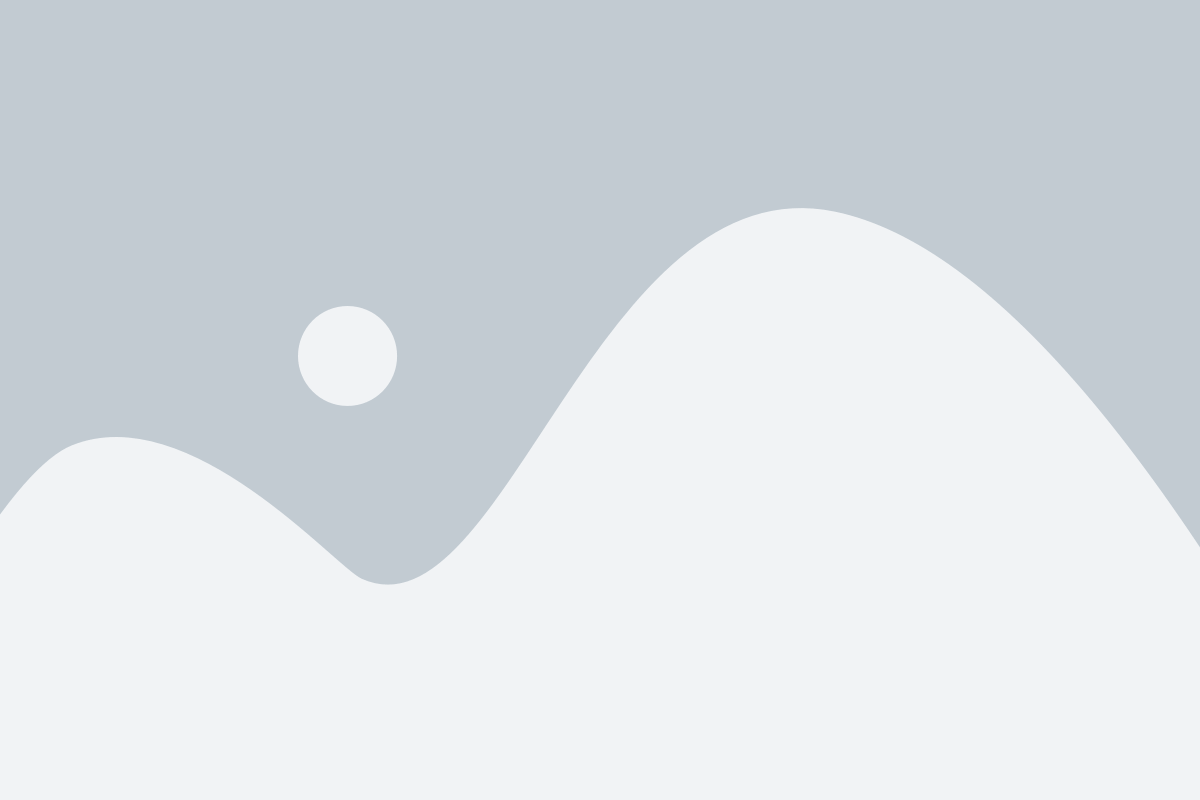
2. Conducting inspection of mooring ropes semi-annually.
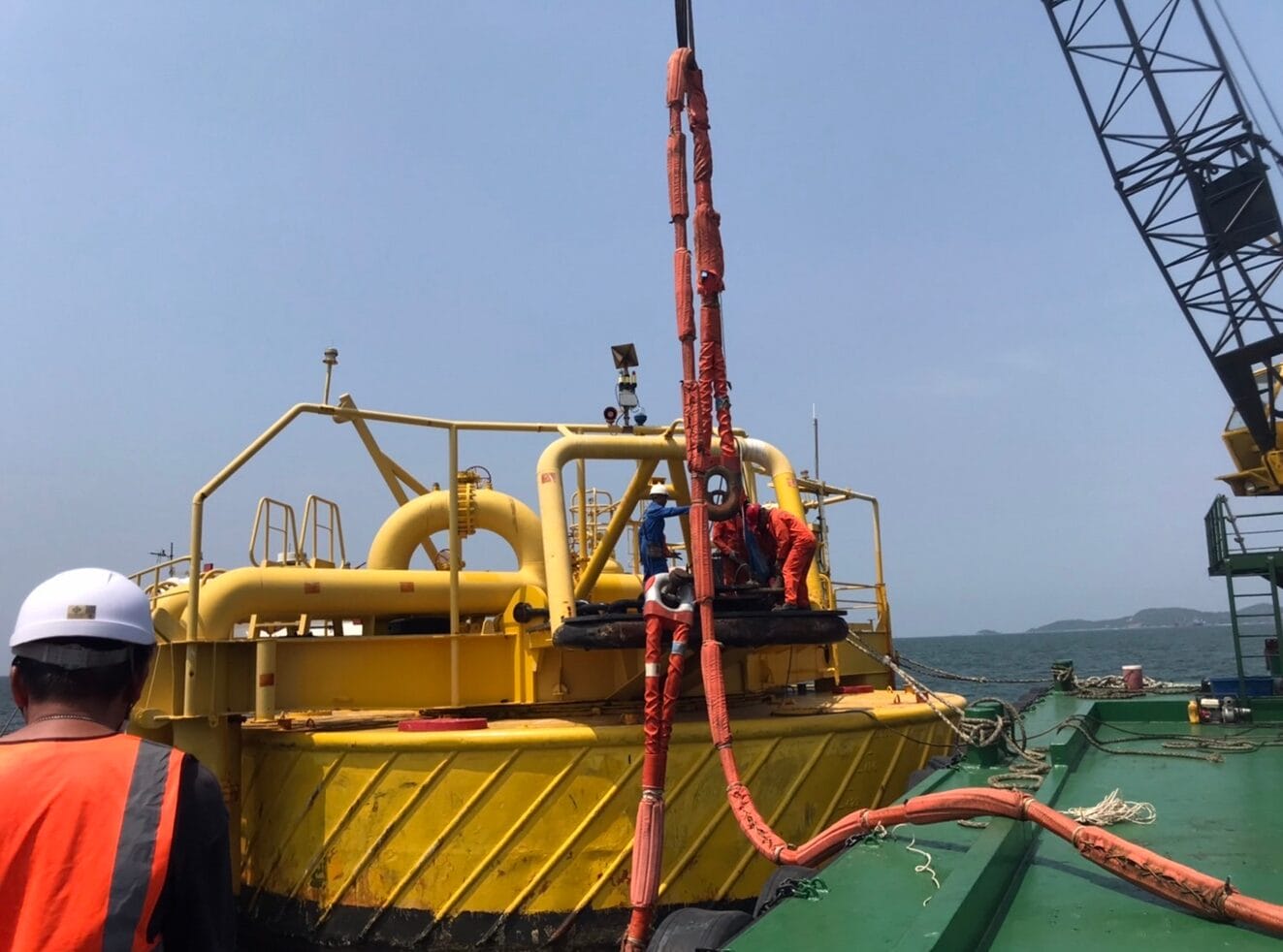
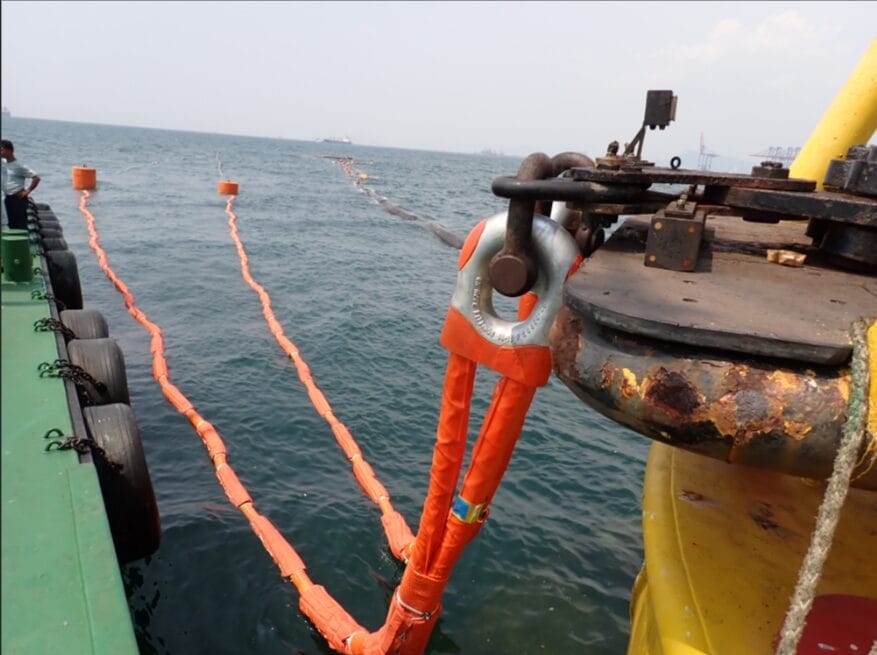
3. Conducting inspections of floating flexible hoses and flanges with the following procedures:
- Conducting diving surveillance every three months.
- Conducting offshore Hydrostatic-leak test annually.
- Conducting onshore inspection and testing every two years in accordance with the international standard OCIMF SMOG 2015.
- Conducting pressure testing of the floating flexible hose system to ensure the complete of the flanges.
- Replacing new floating flexible hoses according to the manufacturer’s recommended interval.
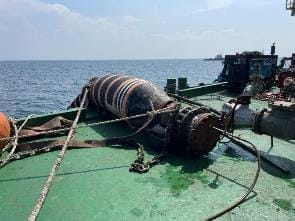
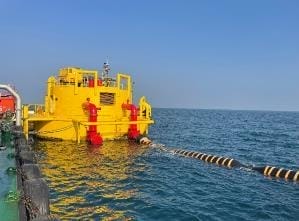
Annual offshore Hydrostatic Testing
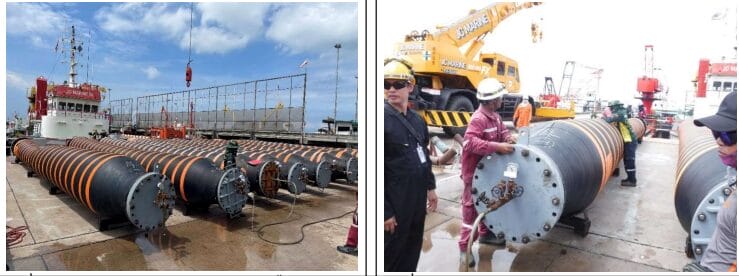
Onshore inspection and testing every two years
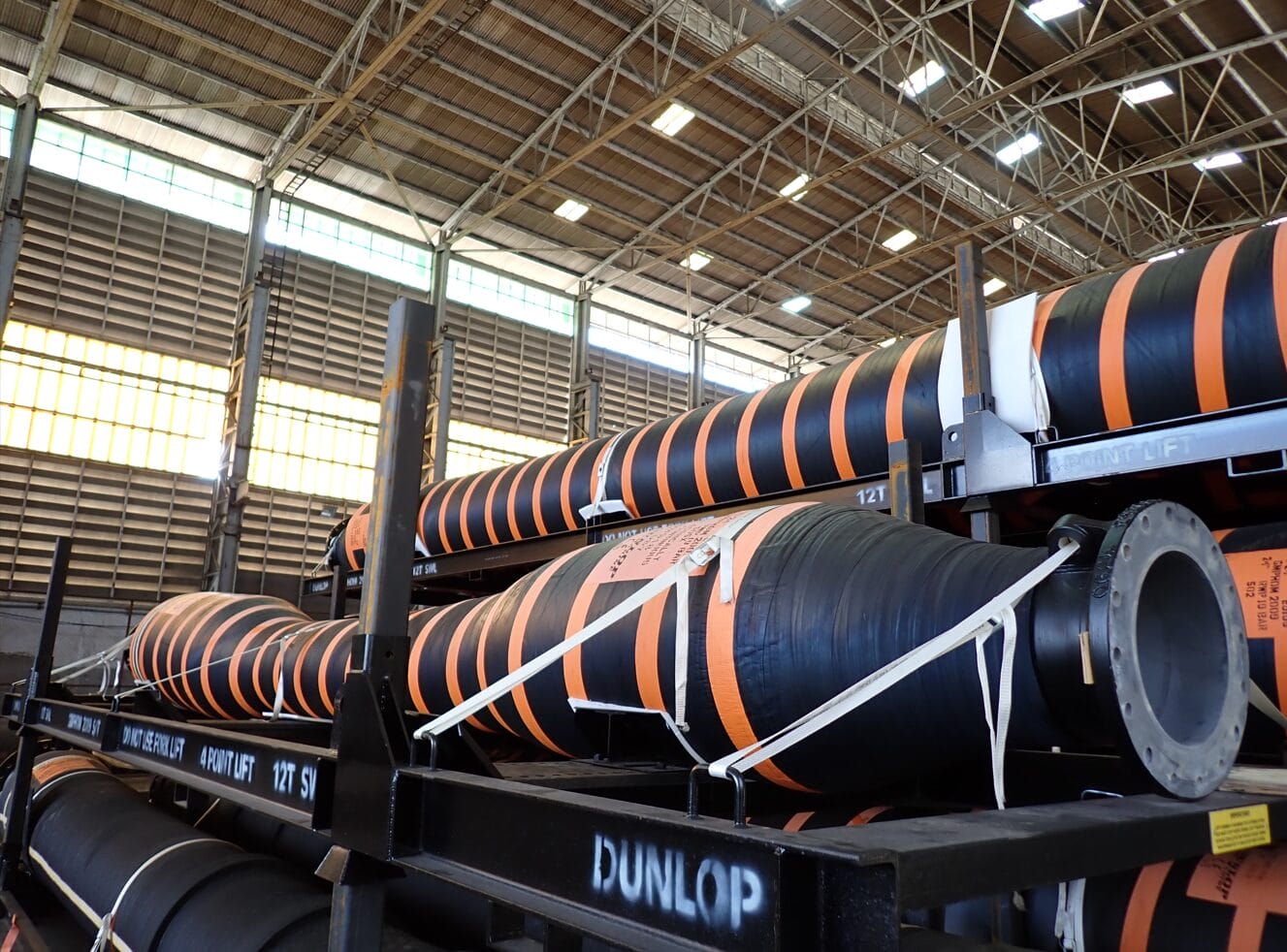
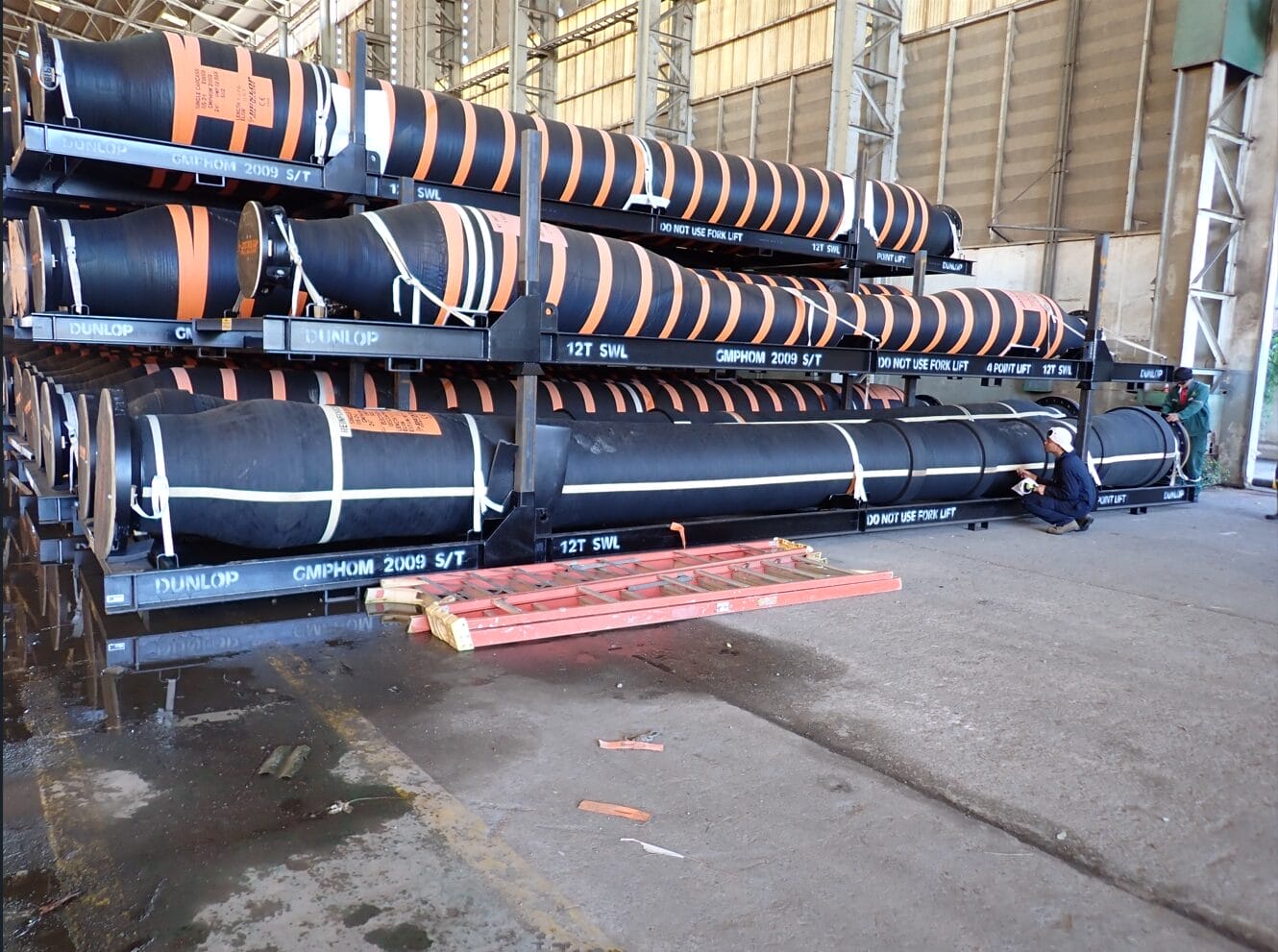
Replacement of new floating flexible hoses following the manufacturer’s recommendation
4. Conducting inspection of mooring system every six months
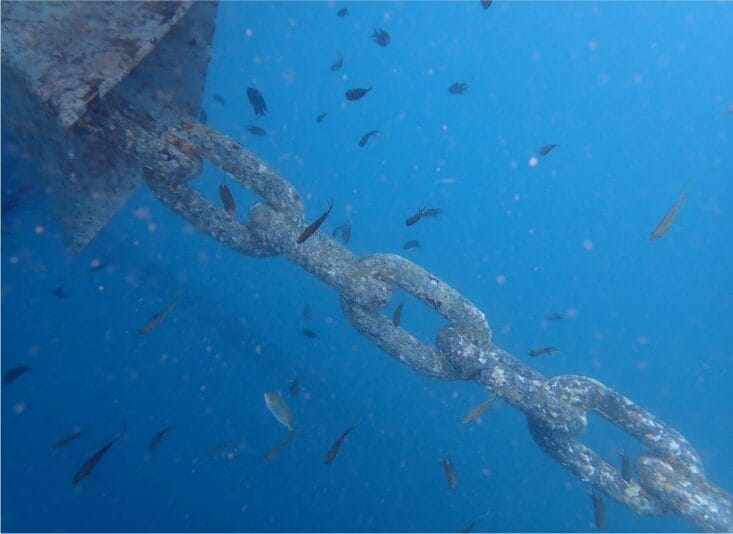
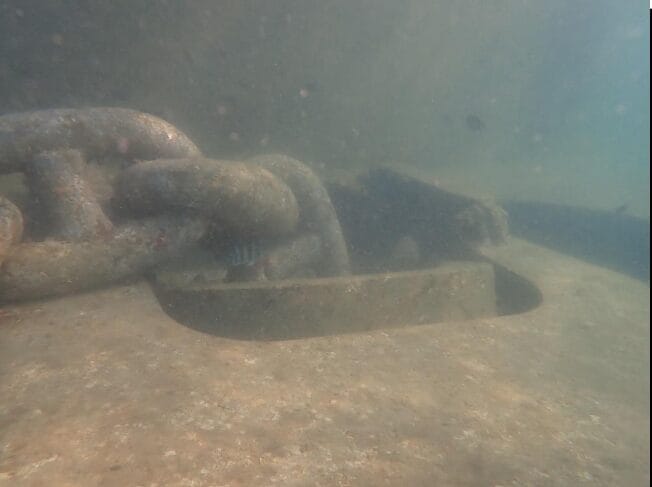
Inspection of mooring system
5. Conducting inspections of flexible submarine hoses for transferring crude oil with the following procedures:
- Performing offshore diving surveillance testing every three months.
- Conducting offshore hydrostatic testing annually.
- Conducting onshore inspections every two years.
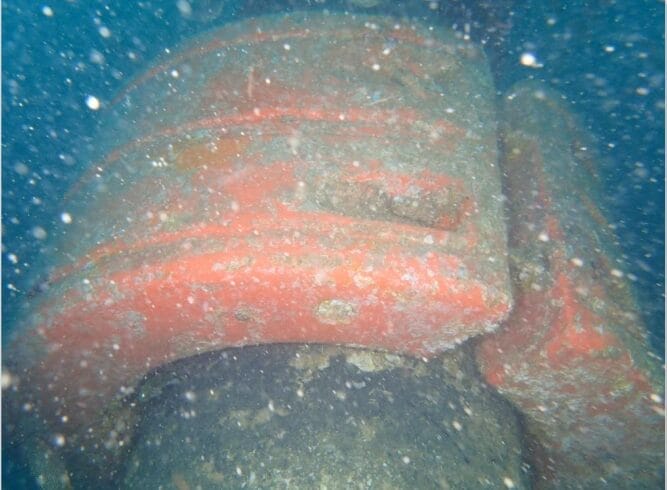
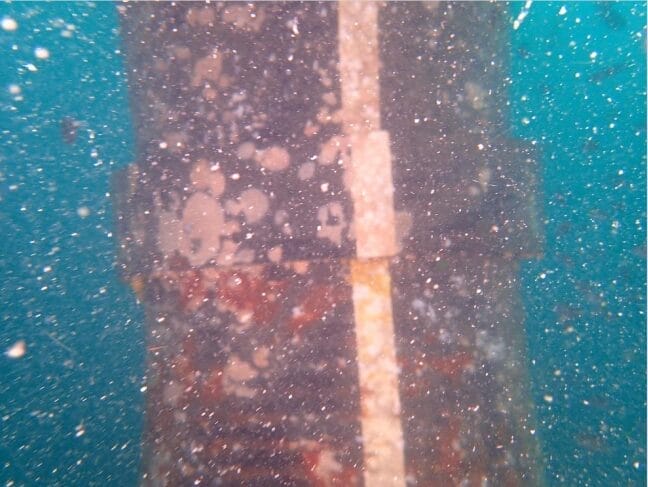
Offshore diving surveillance every three months
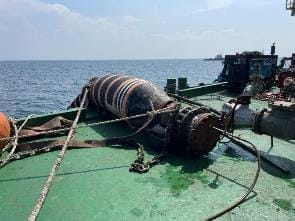
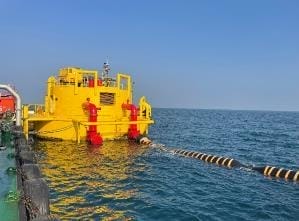
Annual offshore pressure testing of floating and submarine flexible hoses
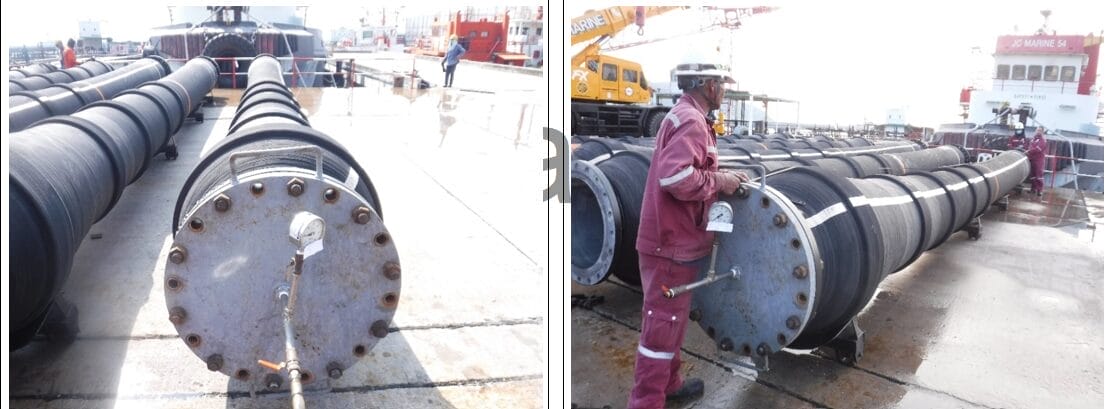
Onshore inspection and testing every two years
6. Conducting inspections of submarine Pipeline End Manifold (PLEM) semi-annually.
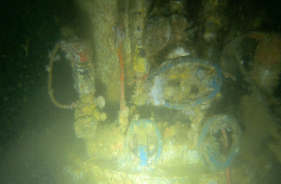
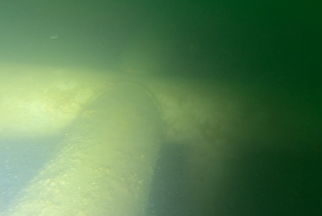
Inspection of submarine structure and control valves
Conducting tanker safety checks for both domestic and international tankers operated at Thaioil Group’s port.
The Port Manager regularly assigns a practitioner to inspect tanker safety. In case where defects are detected, the practitioner will inform the tanker’s captain and manager to address the issues and prevent their recurrence of such defects. The tanker may be temporally suspended under circumstances where the defects are not aligned with the specified safety standards.
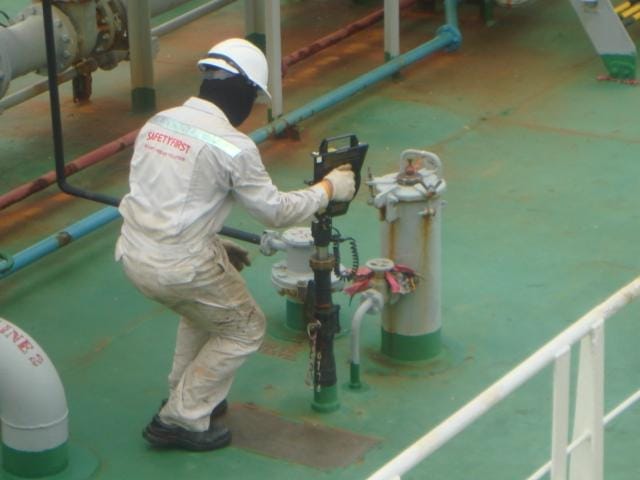
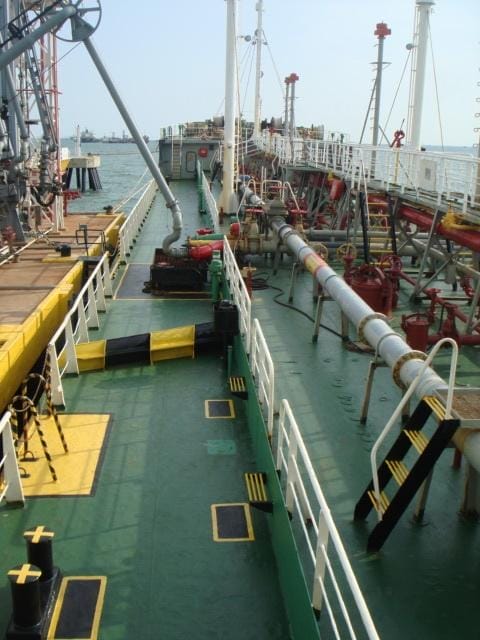
Nominating employees in the port division to attend IESG activities on a regular basis to exchange the marine safety knowledge
Nominating employees in the port division to attend IESG activities on a regular basis to exchange the marine safety knowledge and ensure that the operations are aligned with international standards.
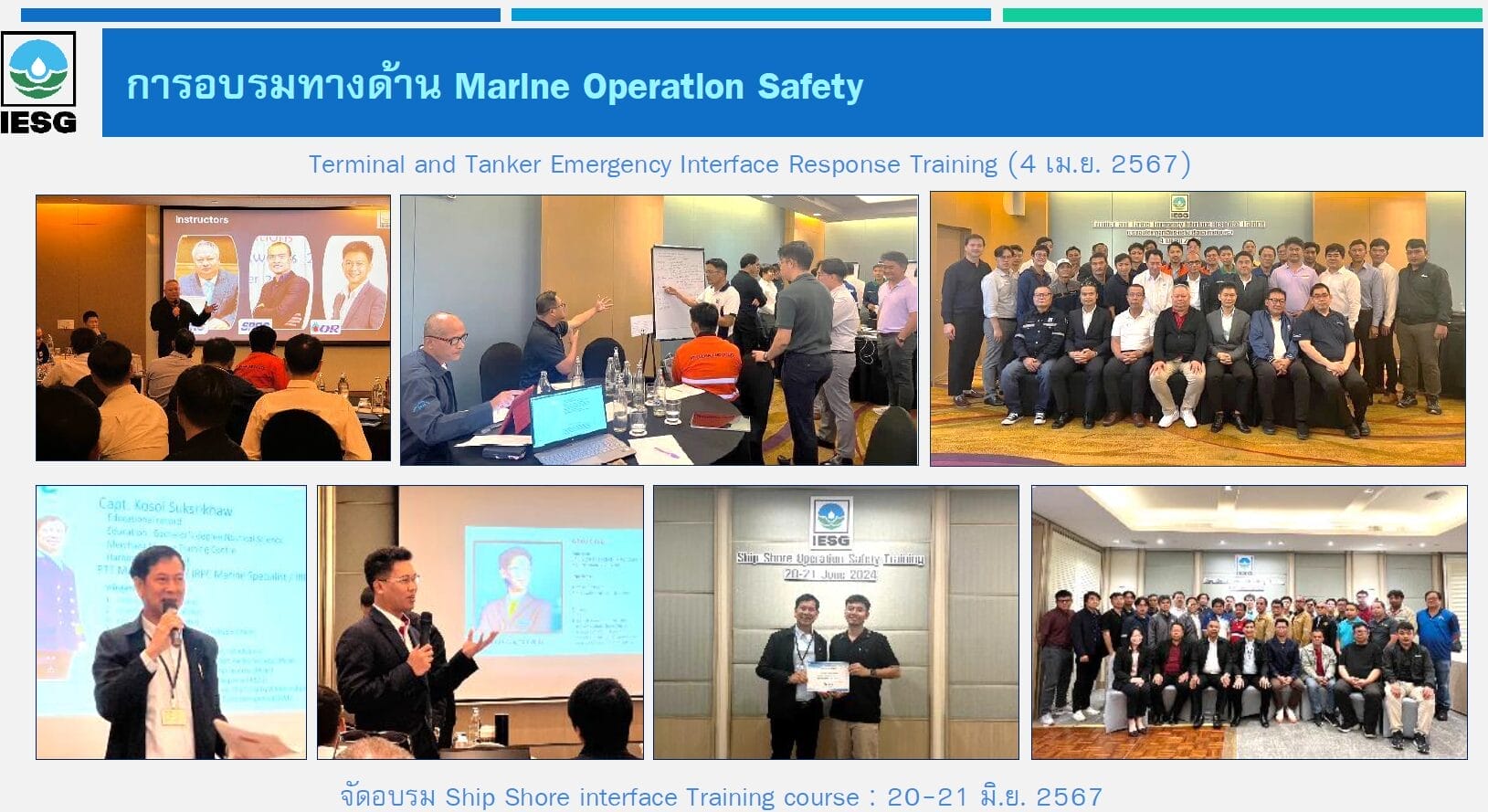
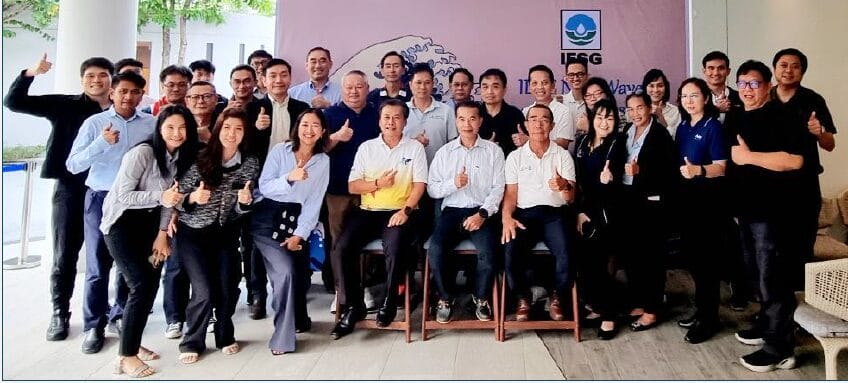
Organizing an annual meeting between IESG and management executives from Thai ship companies.
As Thaioil Group is a member of IESG, the Company share information of ship and port safety, such as updated port rules or identified defects during random ship inspections. This initiative aims to ensure that the Company has effectively implemented corrective actions to improve safety condition in business operations and prevent accidents and pollutions from both ships and ports.
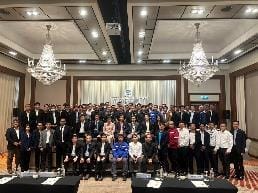
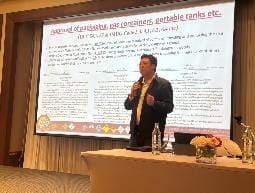
Mitigation
Despite having stringent prevention measures that are aligned with the international standards, Thaioil Group has also developed mitigation measures to address unforeseen incidents, as outlined below:
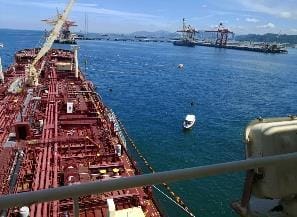
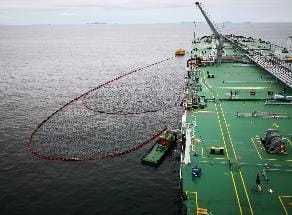
2. The Loading Master, who serves as the head of oil transportation operations for the Company, is required to notify the Emergency Shut Down (ESD) and close all valves on the ship, as well as notifying onshore officers to close all valves to suspend the oil transfer system. This ensures that there is no oil flow and pressure in the system, thereby minimizing the risk of increased oil leakage into the sea.
3. The service boat stationed at the buoy is required to close all valves on both the floating and underwater buoy. This aims to prevent oil from the refinery’s tanks from flowing back into the sea. This action is carried out in accordance with emergency procedures.
4. The Loading Master, who serves as the head of oil transportation operations for the Company, instruct the contractors to deploy Oil Absorbent Booms along the oil pipeline. This is to control oil spills within a limited area and prevent them from flowing to the sea, which could make containment more difficult to control. The preparation measures include conducting at least three training drills per year to maintain readiness for emergency situations. The oil absorbent booms are stored on vessels under the Company’s contract
5. The Company has implemented the safety action in accordance with the action plan to prevent and eliminate water pollution from its operations. This aims to reduce and mitigate environmental impacts until the situation is ultimately under control.
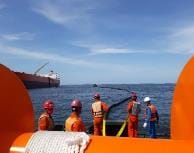
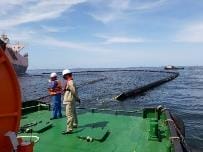
Personnel Development
Thaioil Group prioritizes personnel development to ensure employee are knowledgeable and capable of managing oil and petrochemical spills. In 2024, the Company conducted activities to develop and enhance knowledge of the personnel on oil spill cleaning. The activities are described as follows:
Thaioil Group assigned port captains to attend training at the SmartShip Maritime Simulations
Institute in Australia. The training focuses on piloting vessels into Berths No.7 and 8, which can accommodate ships with maximum capacities of 100,000 tons and 45,000 tons, respectively. The objective of the training is to enhance knowledge and skills in safety manoeuvring large vessels into docks located in constrained spaces.
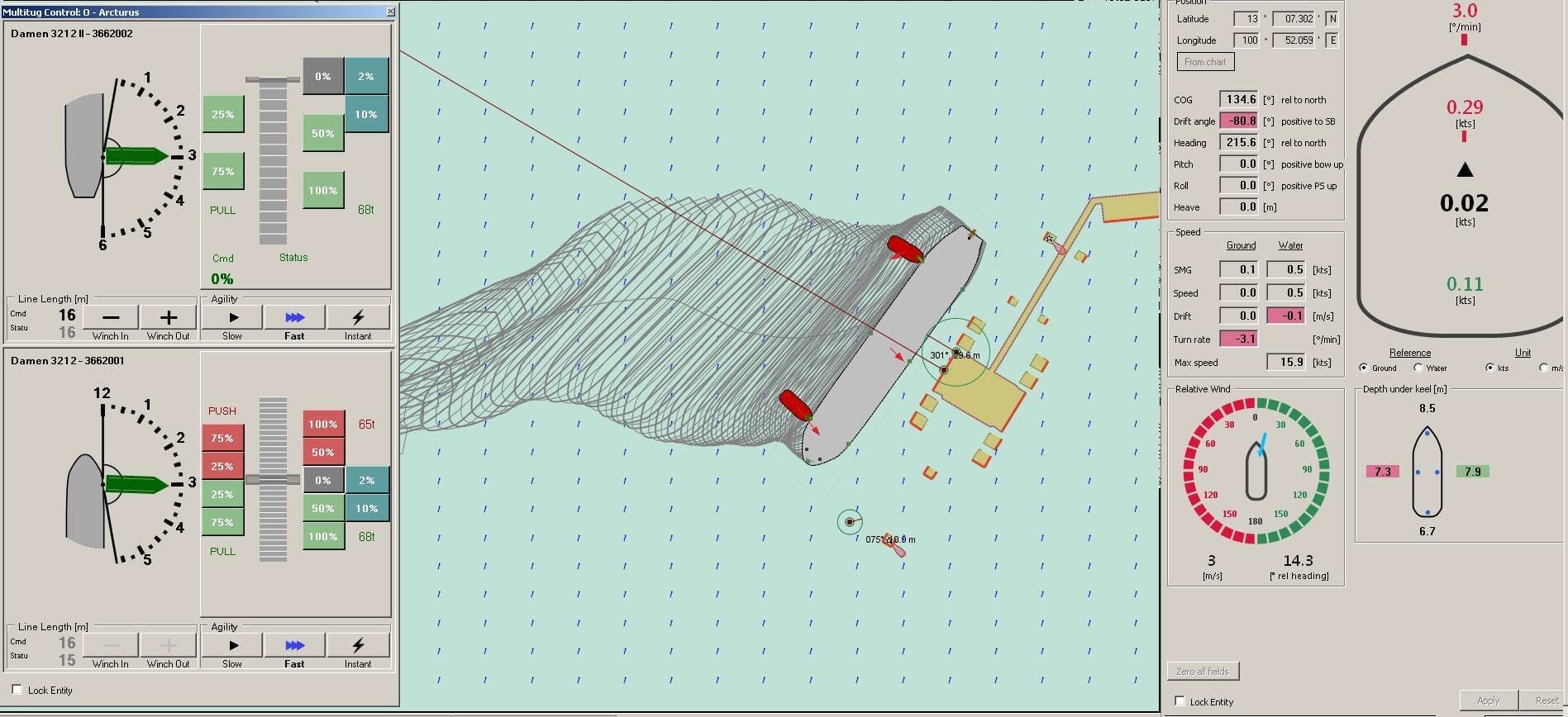
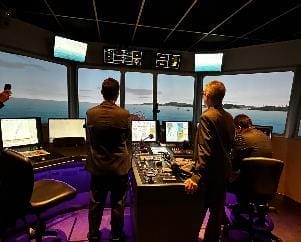
Thaioil Group assigned newly hired port captains who have completed their probationary period
with the Company to attend Ship Handling training at the Warsash Maritime School in the United Kingdom. The training aims to provide an in-depth understanding of the behavior of large oil tankers with a capacity of 300,000 tons and to safely navigate them through channels and manoeuvrer them to moor at SBM in open seas.
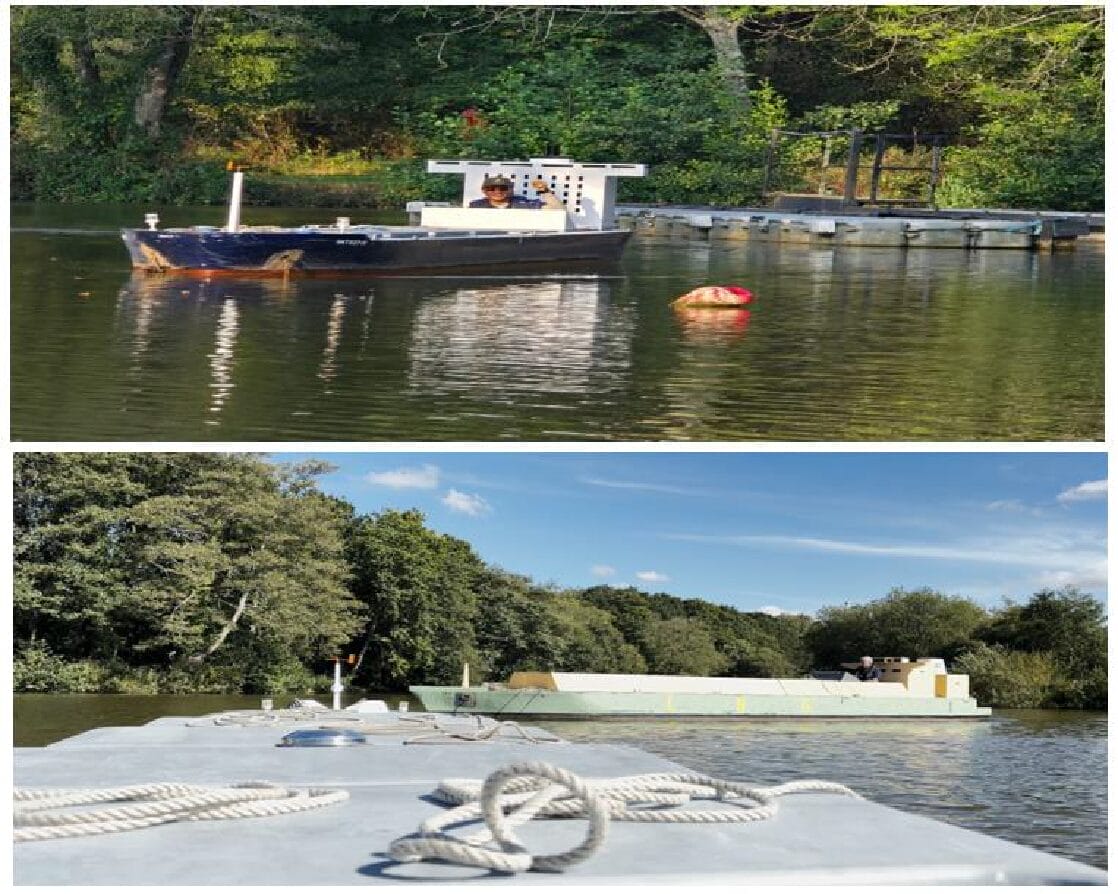
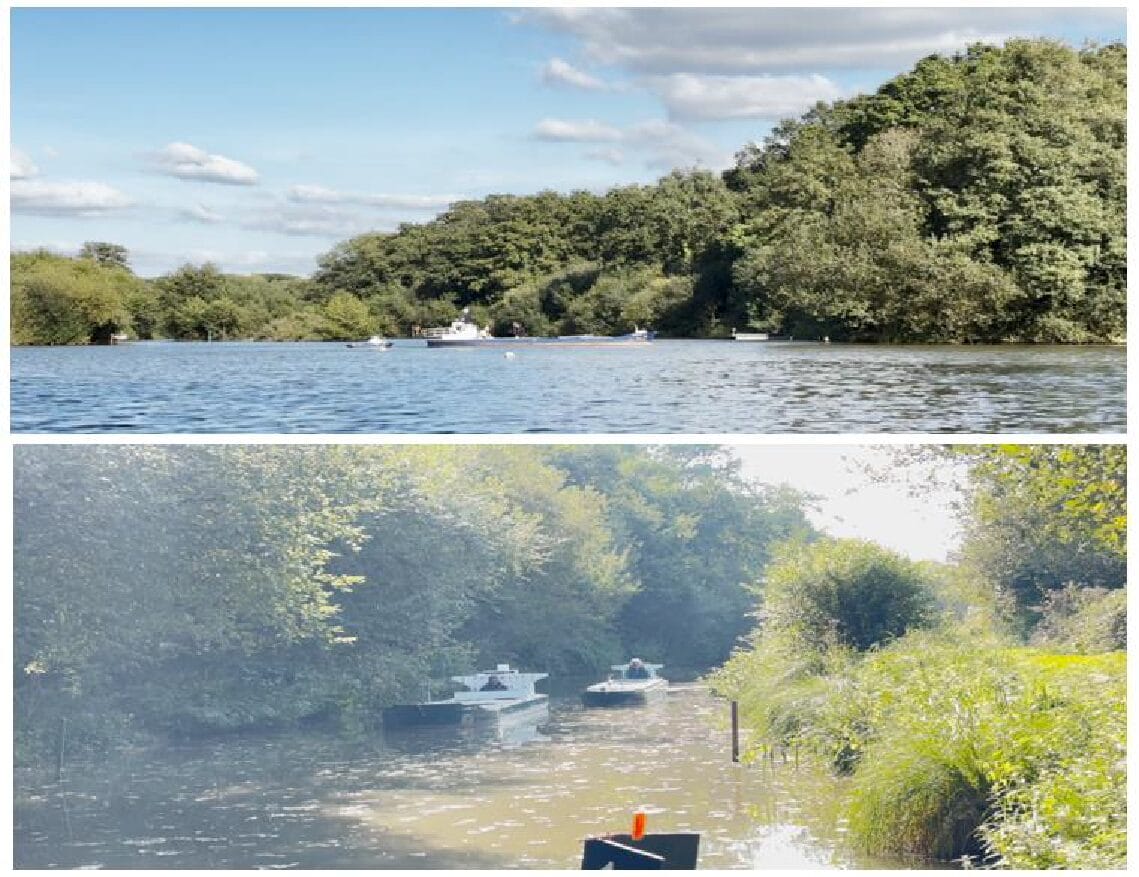
Thaioil Group conducted a marine oil spill response exercise
as a Tabletop Exercise to the on-duty operators assigned in the Company’s Emergency Plan. The exercise has stimulated a scenario in which a submarine hose ruptured at the SBM-1, resulting in an oil spill. The spill widely spread to nearby shellfish farms and fish cages along the coast and reached the shores of Koh Loi and Sriracha Public Park where it is the local fishery area and significant tourist destination that contributes the local economy. In addition, the Company conducted a Shoreline Cleanup Field Exercise for its on-duty emergency response operators. This exercise is complex and involves coordination with multiple provincial and national agencies, such as the Royal Thai Navy, the Pollution Control Department, the Provincial Disaster Prevention and Mitigation Office in Chonburi, and the Provincial Environmental Office, etc.
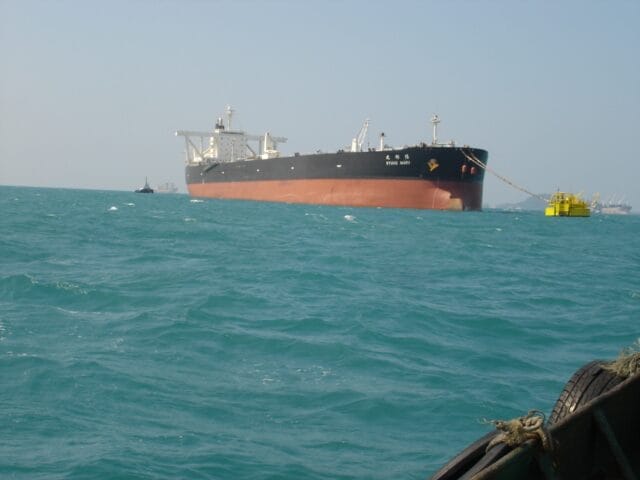
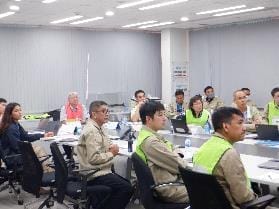
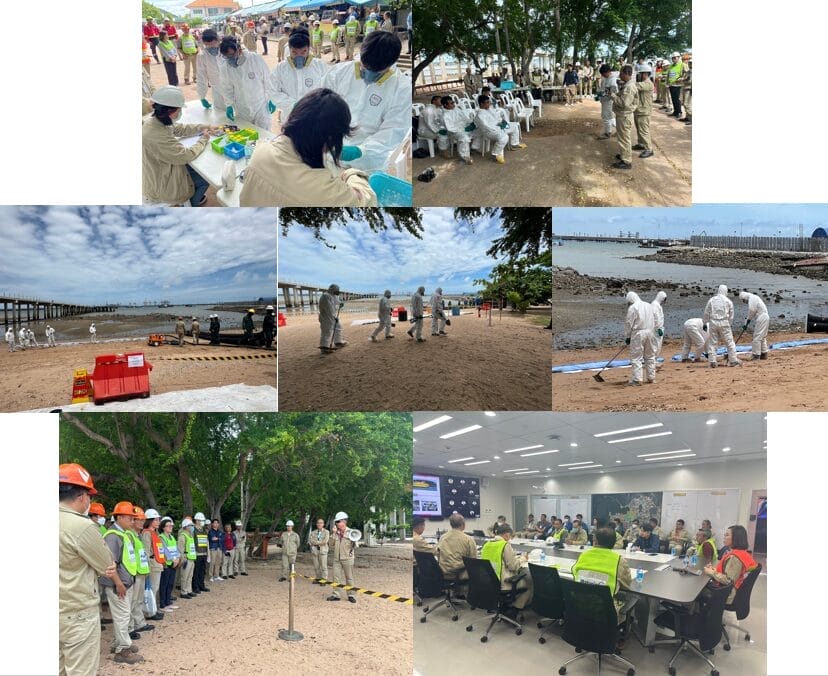
Thaioil Group has collaborated with IESG in the Sri Racha area to conduct a Shoreline Assessment at Koh Sichang beaches.
This aims to understand the conditions of the island, which are vulnerable to the environmental and economic impacts. The assessment is conducted every five years to update the database to the most current information.
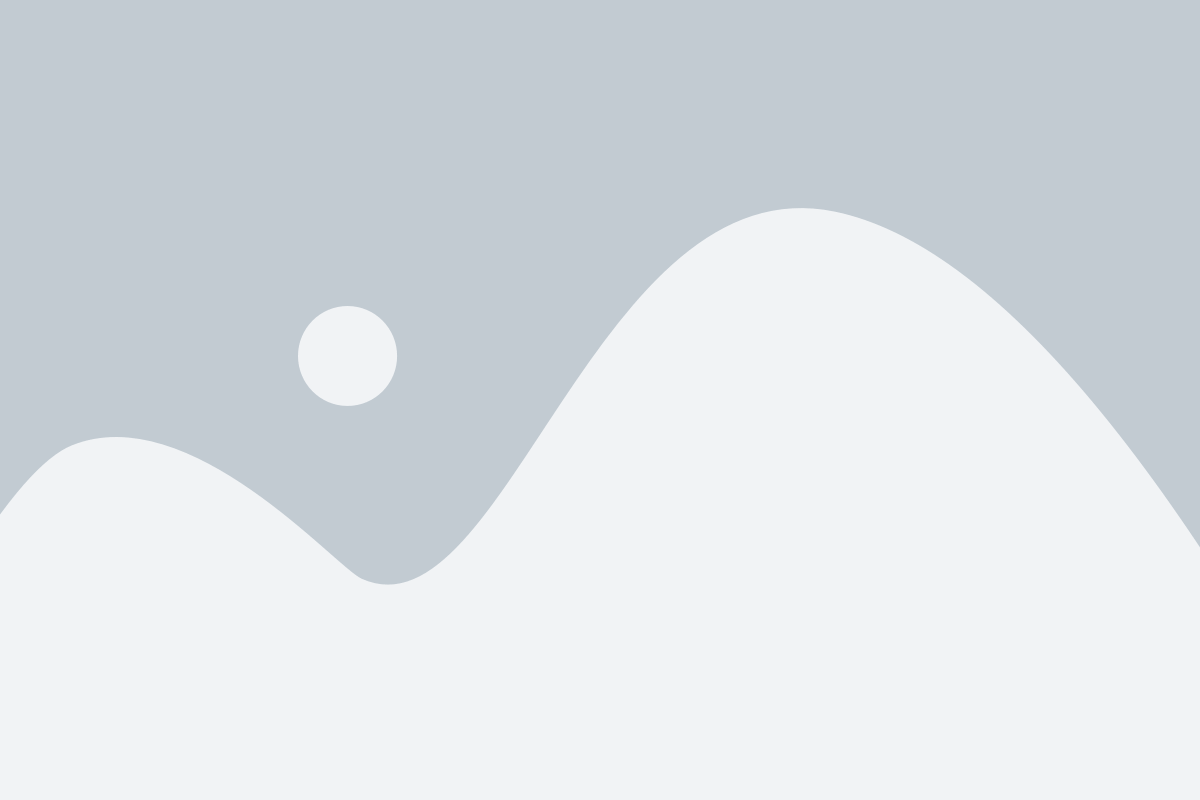
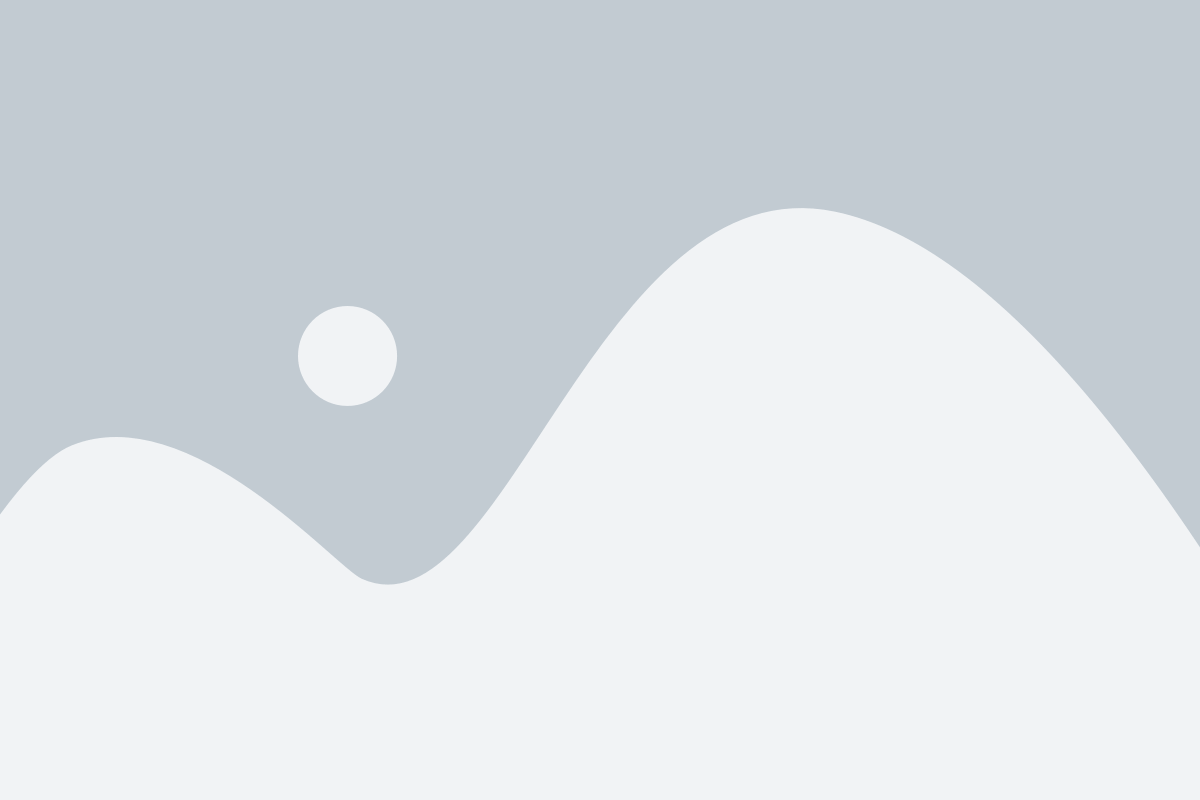
In 2024, Thaioil Group developed key plans as detailed below:
1. Participation in the 14th National Oil and Chemical Pollution Response Exercise (TOC EX-14) in collaboration with the Marine Department, the Royal Thai Navy Region 1, Thai Maritime Enforcement Command Center Region 1 (ThaiMECC Region 1), other government agencies, and the IESG. Moreover, Thaioil Public Company Limited served as the host organization for this exercise.
2. Assigning supervisor-level employees responsible for managing on-site oil spill response operations to attend Oil Spill IMO Level 2 training.
3. Organizing a workshop to enrich knowledge and understanding of marine oil spill or chemical spill response at the first-line level for personnel in the port division.
4. Developing personnel skills, expertise, and knowledge through nominating personnel to participate in trainings or conferences related to marine oil spill prevention and response.
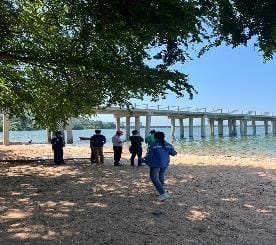
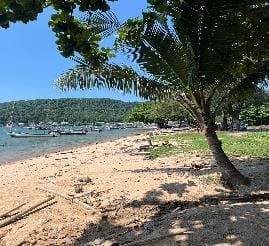
Oil Spill Incident Case Study 2023
Overview of oil spills incident in Chonburi
In 2023, the oil spill incident occurred near the Single Buoy Mooring (SBM-2) of the Thaioil refinery in Sriracha, Chonburi, during the late hours of the night on September 3, 2023, there were approximately 60,000 liters of oil spills, or approximately 377.39 barrels. Oil spills can be contained and resolved rapidly without oil stain shoreline. However, there is no legal proceeding matter and sanction in relation to oil spills in Chonburi. The case is currently under investigation.
Root causes of the spill incident
The incident occurred due to the broken hose in the second section (counting from the SBM-2 buoy towards the ship), causing a crude oil leak. The cause of leakage is under investigation by a government-appointed committee.
Implemented measures
Thaioil has implemented four management measures including (1) Prevention, (2) Mitigation (3) Equipment inspection, and (4) Personnel development.
1. Department of Engineering and Marine Movement and Logistic implemented the prevention measures which complied with Oil Company International Marine Forum (OCIMF) standard i.e. Single point mooring Maintenance and Operations Guide (SMOG), International Safety Guide for Oil Tanker and Terminal (ISGOTT) and Guide to Manufacturing and Purchasing Hoses for offshore Moorings (GMPHOM) are as follows:
- The design and construction of mooring buoys, as well as floating and subsea piping systems meet international standards.
- Adopt crude oil pumping and receiving protocols that align with international standards.
- Monitor and maintenance of relevant equipment.
2. Emergency and Crisis Management Team, consisting of Refinery duty team and communication teams, mitigate the impacts of the incidents through measures as detailed below:
- Adopt manual and contingency plans.
- Provide training in Oil Spill International Maritime Organization (IMO) Level 1-3 and ICS 100/200/300 to an operation team and party concern i.e. Environment, Safety , Security.
- Prepare and preventive maintenance oil spill equipment to be available on marine vessels and warehouses ready for use.
- Preparedness Oil spill response for Emergency Response Team(ERT), Mobilization oil spill equipment, Communicate with external party and Cooperation with Government sector i.e. Royal Thai Navy Fleet 1, Marine Department.
3. Department of Inspection and Equipment Integrity, evaluating the effectiveness of its existing procedures and has taken proactive steps to enhance the quality and integrity of Bouy, piping and hoses. All the quality and assurance process will be started from vendor selection, manufacturing, receiving, interval inspection until the end of service life which all processes are complied with the latest international standards and vendor guidelines, as detailed below:
- Evaluate and refine the storage and transportation processes for floating hoses and subsea hoses to avert wear and tear, damage, or any other issues that could compromise their longevity. This includes thorough assessments by independent third-party experts.
- Reassess the service life of floating hoses and subsea hoses, based on current operational conditions and adhering to the manufacturer’s guidelines. This evaluation considers factors, such as usage frequency, environmental conditions like sea waves, the type of crude oil being transported, and potential contamination risks. This process has been implemented by the internal inspection team.
- Explore alternative types of floating hoses and subsea hoses to diminish the risk of crude oil spill incidents
4. In 2024, Department of Marine Movement and Logistic provided various trainings:
- Ship handling course (Manned Model) at Warsash Maritime school, England.
- Ship handling simulation course at Smartship Maritime Simulations, Australia.
- Spill site supervisor (IMO Level 1)
In addition, the Company plan to participate with Oil Industry Environmental Safety Group Association in Sriracha area (IESG-SASC) to conduct the oil spill exercise shoreline clean up in 2024. This is a joint exercise with Thai Oil Public Company Limited, PTTOR Public Company Limited, and Bang Chak Sriracha Refinery (BSRC-Refinery) Company Limited, which will be hosted by Thai Oil Public Company Limited. The strengthened process and measures will be applied in this exercise.
Response and remediation
Moreover, the Emergency and Crisis Management Team has managed responsive actions to minimize the impacts of the incidents. Once the incident occurred,
- Thaioil swiftly responded with support from government and private entities to manage and resolve the situation rapidly, safely and effectively. no oil stain shoreline Thaioil conducts engagement with publics including community, investors and shareholders to build trust and compensation to those which are negatively affected by the incident with approximately 47.5 million THB.
- Thaioil continuously monitors ecological impact and biodiversity and has assigned the environmental management department to monitor and restore biodiversity at site affected by oil spills.
Key Highlighted Projects
In 2024, Thaioil Group launched development projects and upgraded its management of abnormal operating conditions and the environmental emergency situations. For example:
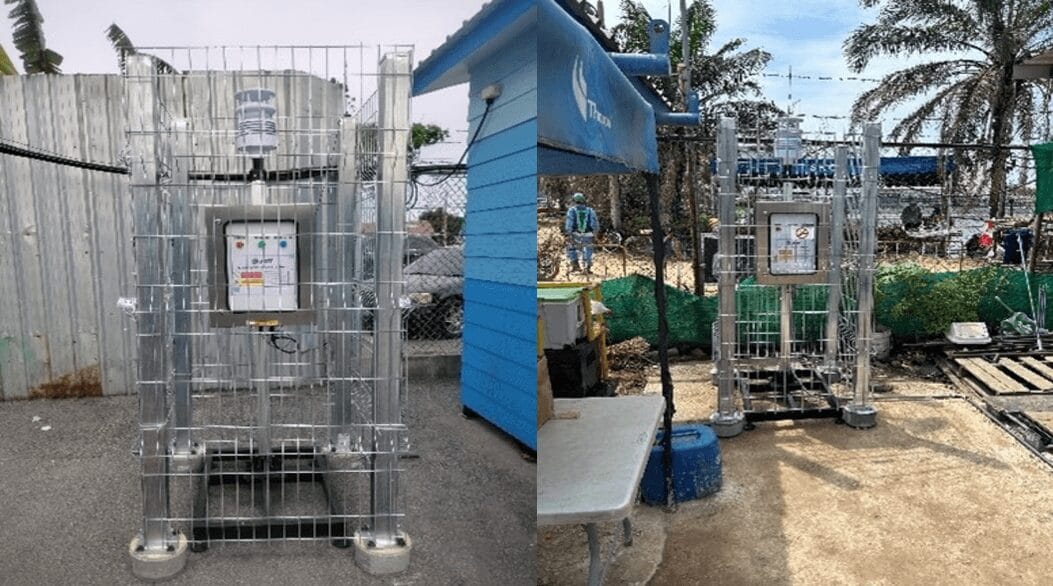
Thaioil Group collaborated with the innovation department of PTT Public Company Limited to conduct the study and experiment of the Electronic Nose (E-Nose)
2024
Performances
Vel pretium dolor tellus id purus felis tellus cursus. Amet turpis vel enim aliquet maecenas. Egestas nulla urna suspendisse cursus aliquam mauris facilisis.
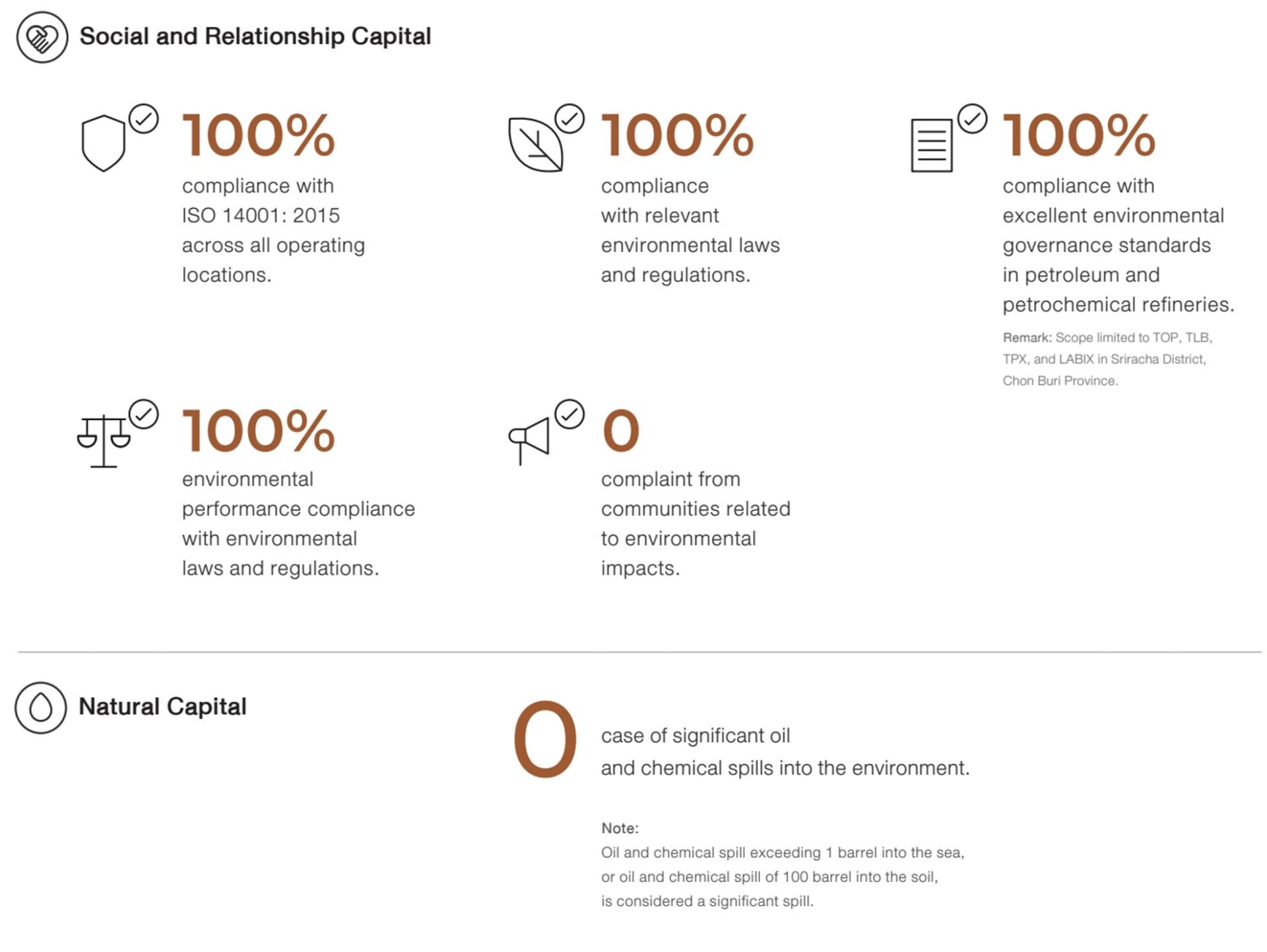
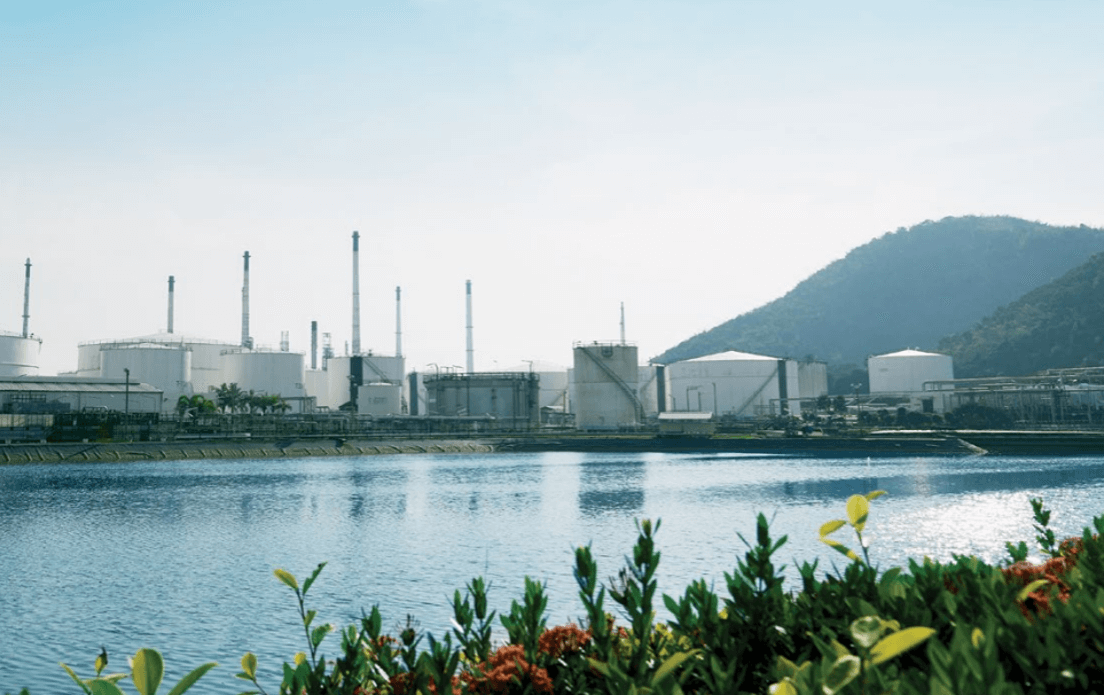
Management Approach
Thaioil Group is committed to minimizing environmental impact to facilitate continuous business, while maintaining environmental consciousness alongside surrounding communities. To achieve this, the Company has established targets for controlling air quality, including Nitrogen Oxides (NOx), Sulphur Oxides (SOx), Volatile Organic Compounds (VOCs), and Particulate Matter (PM). Starting from the design phase, the Company selects and installs high-efficiency technologies that meet international standards to control its production processes. The Company also monitors and measures air quality at its sources and in the surrounding areas on a regular basis in accordance with a predetermined schedule. The Company also uses an air quality monitoring system that displays real-time results and tracks the performance of air quality against international best practices. The Company’s environmental management system and performance is audited and certified by an external party on an annual basis.
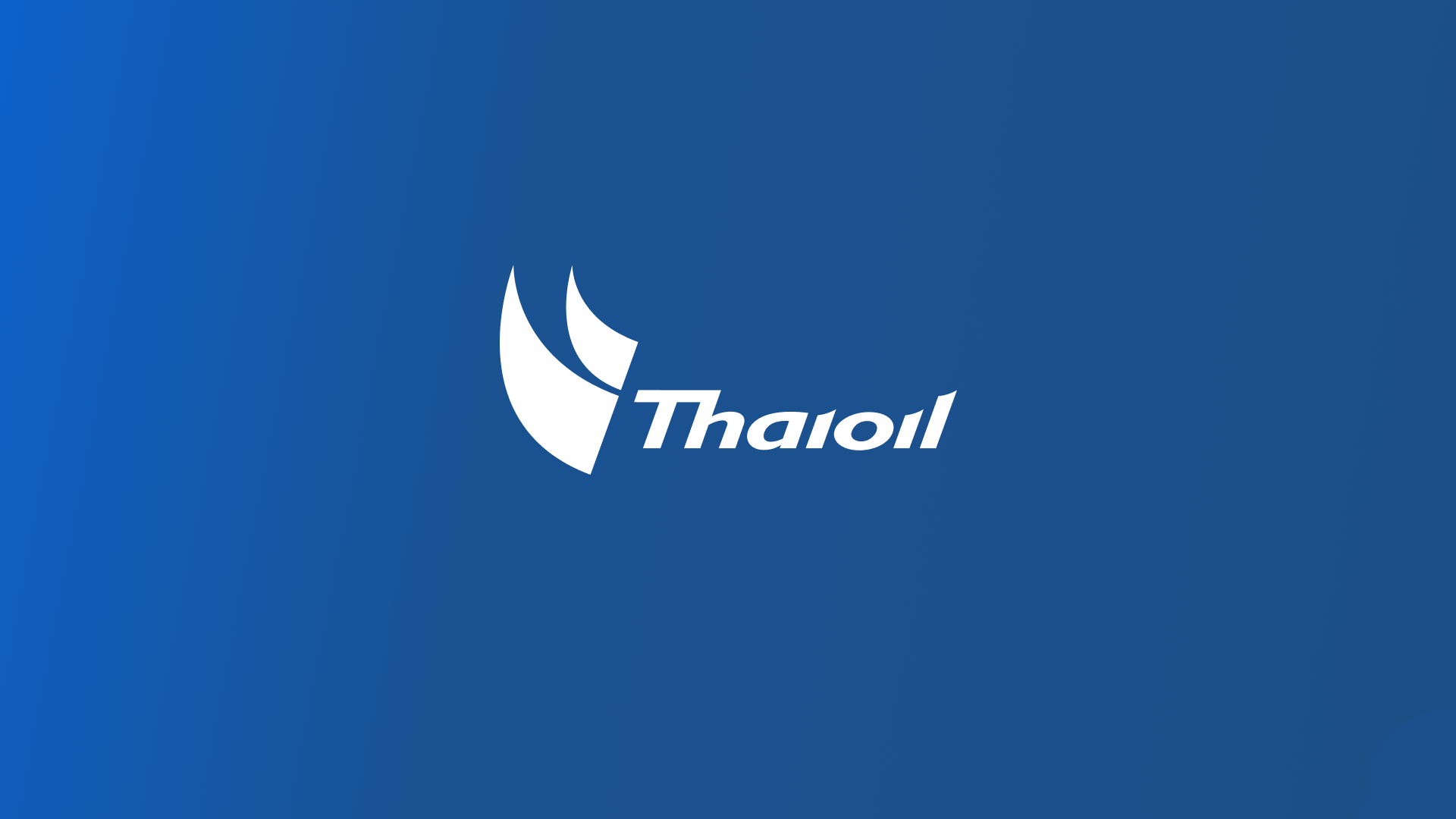
NOx and SOx Emissions Management
Thaioil Group assesses environmental impacts and determines preventive measures to control NOx and SOx emissions from the production process. The primary source of emissions is from fuel combustion. To control and minimize these emissions, the Company has installed high-quality technology that is internationally recognized and continuously operates the Sulphur Recovery Unit (SRU) system. The SRU system can effectively convert Sulphur from waste gases into a liquid product for use in other industries instead of emitting it into the environment. Furthermore, the Company upgraded all burners to Ultra-Low NOx in 2010 to effectively reduce Nitrogen Oxides emissions from combustion. The Company also controls the usage of low-polluting fuel over the high-polluting fuel and regularly monitors the smoke from combustion (White Smoke Monitoring) and manage irregularities from the early stages to avoid impacts on the community. Moreover, Thaioil Group measures the air quality both at the sourc and in the surrounding communities by using advanced technologies, such as the Continuous Emission Monitoring System (CEMS) and the Air Quality Management System (AQMS), respectively. The air quality is also measured and audited by an external party, and reported daily in the Environmental Daily Dashboard. Consequently, in 2024, Thaioil Group was able to control Nitrogen and Sulfur Oxides emissions at levels better than the required standards and set targets.
Despite the increasing trend of our sulfur dioxide (SOx) emissions in 2023, the company is implementing a project called CFP to expand our refining capacity from 275,000 barrels to 400,000 barrels per day. This expansion will achieve economies of scale, reduce production costs, and allow for greater flexibility in processing different types of crude oil. Thus, the company will refine more heavy crude oil, up to 40-50 percent more, and turn fuel oil into more valuable products like jet fuel and diesel. By doing this, we expect to use less fuel oil and lower our SOx emissions in the future.
In addition, in 2024, Thaioil Group implemented additional projects to control SOx and NOx emissions as follows:
- Thaioil Group recognizes the importance of controlling air quality emitted from stacks across various parameters, such as Sulfur Dioxide (SOx), Nitrogen Oxides (NOx), Carbon Monoxide (CO), and total suspended particulates (TSP). Therefore, Thaioil Group has installed the Continuous Emission Monitoring System (CEMS) to report emission values 24/7 for all stacks, with the installation expected to be completed by 2027.
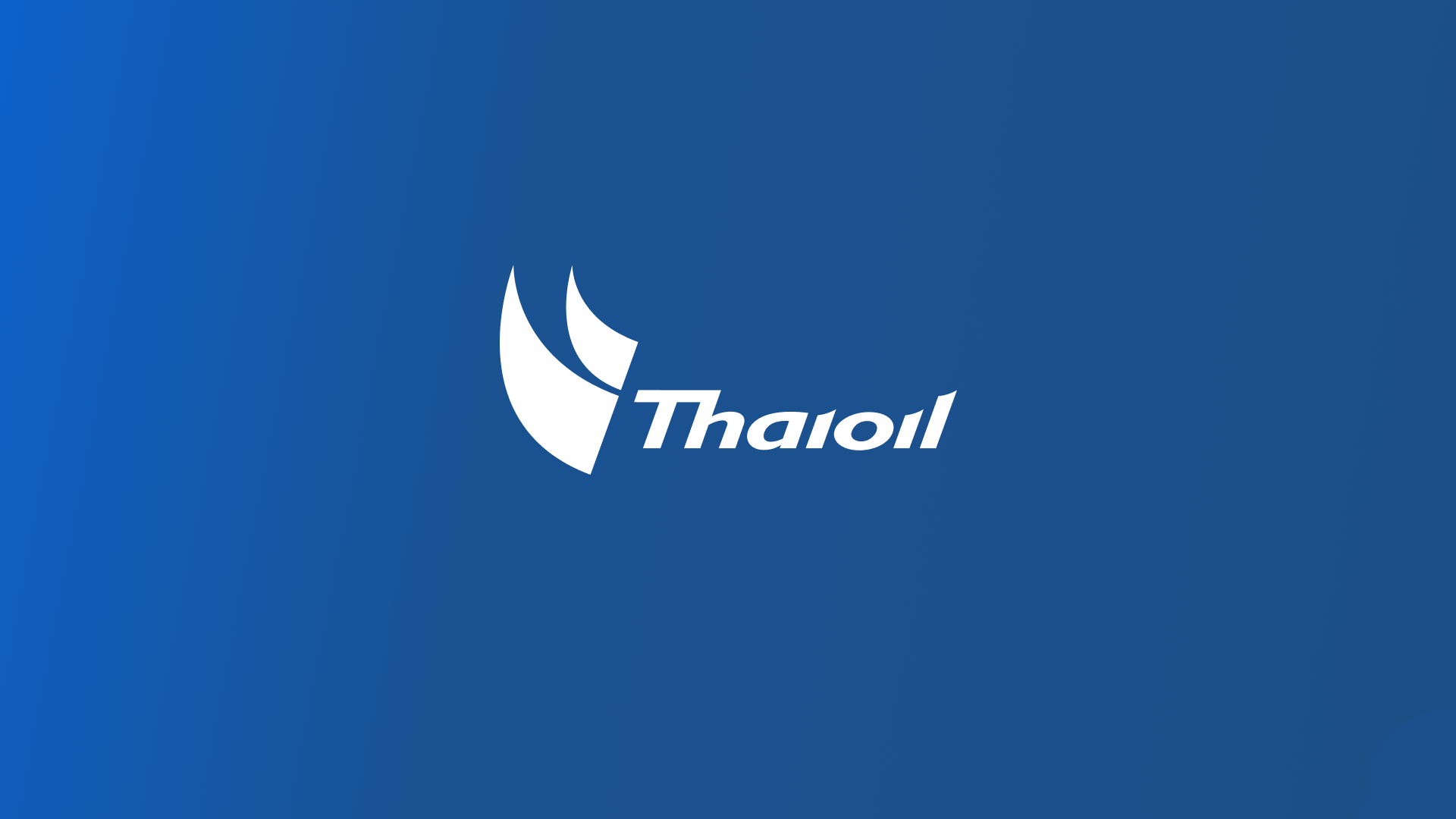
VOCs Emissions Management (VOCs)
Thaioil Group manages Volatile Organic Compounds (VOCs) emissions through environmental impact assessment. The Company implements preventive and monitoring measures of VOCs emissions from various sources within the production process, including flares, combustion, tanks, loading, effluent treatment plants, and fugitives, through operational excellence management as follows:
-
Flares and Fuel Combustion: The Company monitors flare efficiency, maintenance process, and implements controls to prevent undesirable incidents that may emit VOCs emissions from the combustion tower.
-
Tanks and Loading processes: The Company selects appropriate storage tanks for each substance or fuel being stored, and installs a Vapor Recovery Unit (VRU) with a high efficiency of up to 99% to treat VOCs during product transfer.
-
Effluent Treatment Plants (ETP): The Company regularly tracks and monitors VOCs emissions to improve its wastewater treatment system. The ETP Cover Project has been initiated and is now in the process of installing an ETP Cover system to reduce VOCs emissions into the environment.
-
Fugitives from operational processes: The Company controls and monitors ventilations through the VOCs emission leak detection camera. The camera helps identify leak points in accordance with regulations, international laws, and standards specified in the US Environmental Protection Agency (US EPA) since 2012. This provides opportunities for further improvement to prevent fugitive emissions.
-
VOCs Reduction Measures in Maintenance: The Company has amended the maintenance work procedures to align with best practices and ensure that VOCs emissions are controlled below legal requirements in all activities. Moreover, VOC measurements are conducted along the perimeter of the Thaioil Group during maintenance to monitor and ensure that VOC levels remain within standard limits throughout the maintenance period.
- After Thaioil Group developed the “Scrubber Unit Machine” by adopting Wet & Dry Scrubber Technologies to assist in reducing the VOCs emissions to below 500 ppm before opening oil storage tanks. This machine has been effectively used in oil tank maintenance process. Furthermore, the Innovation Department has developed a chemical agent that accelerates the reduction of VOCs more rapidly by adding the chemical into the Wet Scrubber. The initial phase is currently under trial, and upon successful completion, it will be implemented in the annual major maintenance period commencing in 2025.
Particulate Matter (PM) Management
“PM2.5 Taskforce” consistently monitors and develops management approach to drive and communicate activities to control PM2.5 under the 4C measures (Control, Contain, Clean, and Check). These approaches have been implemented to reduce environmental impact at the source, such as office buildings, production processes, construction projects, and community areas, as well as supporting governmental activities and measures. Besides, the Company regularly measures PM10 and PM2.5 by using the Air Quality Management System (AQMS) and undergoes audits by external parties. Likewise, the Company regularly communicates the PM2.5 management through ENVI E-newsletter to all employees.
In 2024, Thaioil Group conducted stack sampling measurement, in accordance with the methodologies stipulated within the Environmental Impact Assessment (EIA), yielded a particulate matter emission rate of 226 metric tons per year. To manage this, Thaioil Group implemented additional projects under the 4C measures as follows:
• C-1 Control: The Company maintained the air quality at a higher level than standards and legal requirements. Several activities were undertaken to limit the use of vehicle and road usage, including the promotion of carpool campaign, the change of carpool vehicles to electrical vehicles, and the adoption of “Fast & Flow” strategy to manage traffic flow. The Company also monitored and controlled the vehicles’ conditions and their black smoke, as well as ensuring the proper use of dust covers of dusty material on dump trucks.
• C-2 Contain: The Company organized an activity to control the dust pollution levels on walkways, aiming to minimize dust dispersion and accumulation. The activities included installing a dust collection net, using tarp covers to prevent dust from transport vehicles, setting up wheel washes in the construction area, installing water spray, and providing dust protection masks for employees and contractors working in risk areas.
• C-3 Clean: The Company established cleaning initiatives in buildings, lorry loading areas, and construction sites. These initiatives included activities such as carpet cleaning, air conditioner cleaning, 5S activities, Big Cleaning Day, and regularly cleaning the road within Thaioil Group premises and surrounding communities. In addition, the Company supported government initiatives to control dust levels on Sukhumvit Road by spraying water.
• C-4 Check: The Company conducted regular site audits to monitor dust pollution levels by tracking data from the Pollution Control Department station, TOP AQMS lorry station, and PM2.5 NONG PIM detectors to assess air quality both indoors and outdoors.
C-1 Control
The Company maintained the air quality at a better level than standards and legal requirements. Several activities were undertaken to limit the use of vehicle and road usage, including the promotion of carpool campaign, the change of carpool vehicles to electrical vehicle, and the adoption of “Fast & Flow” strategy to manage traffic flow. The Company also monitored and controlled the vehicles’ conditions and their black smoke, as well as ensuring the proper use of covering of dusty material on dump trucks.
C-2 Contain
The Company organized an activity to control the level of dust on walkways, aiming to reduce diffused and accumulated dust. The activities included installing a dust collection net, using tarp covers to prevent dust from transport vehicles, setting up wheel washes in the construction area, installing water spray, and providing dust protection masks for employees and contractors working in risk areas.
C-3 Clean
The Company established cleaning initiatives in buildings, lorry loading areas, and construction sites. These initiatives included activities such as carpet cleaning, air conditioner cleaning, 5S activities, Big Cleaning Day, and the TOP Green Road. In addition, the Company supported government initiatives to control dust levels on Sukhumvit Road by spraying water.
C-4 Check
According to the site audit measures, the Company tracked dust pollution levels from the Pollution Control Department station, including the TOP AQMS lorry station, and used a PM2.5 NONG PIM detector to assess air quality both indoors and outdoors.
2024
Performances
Vel pretium dolor tellus id purus felis tellus cursus. Amet turpis vel enim aliquet maecenas. Egestas nulla urna suspendisse cursus aliquam mauris facilisis.
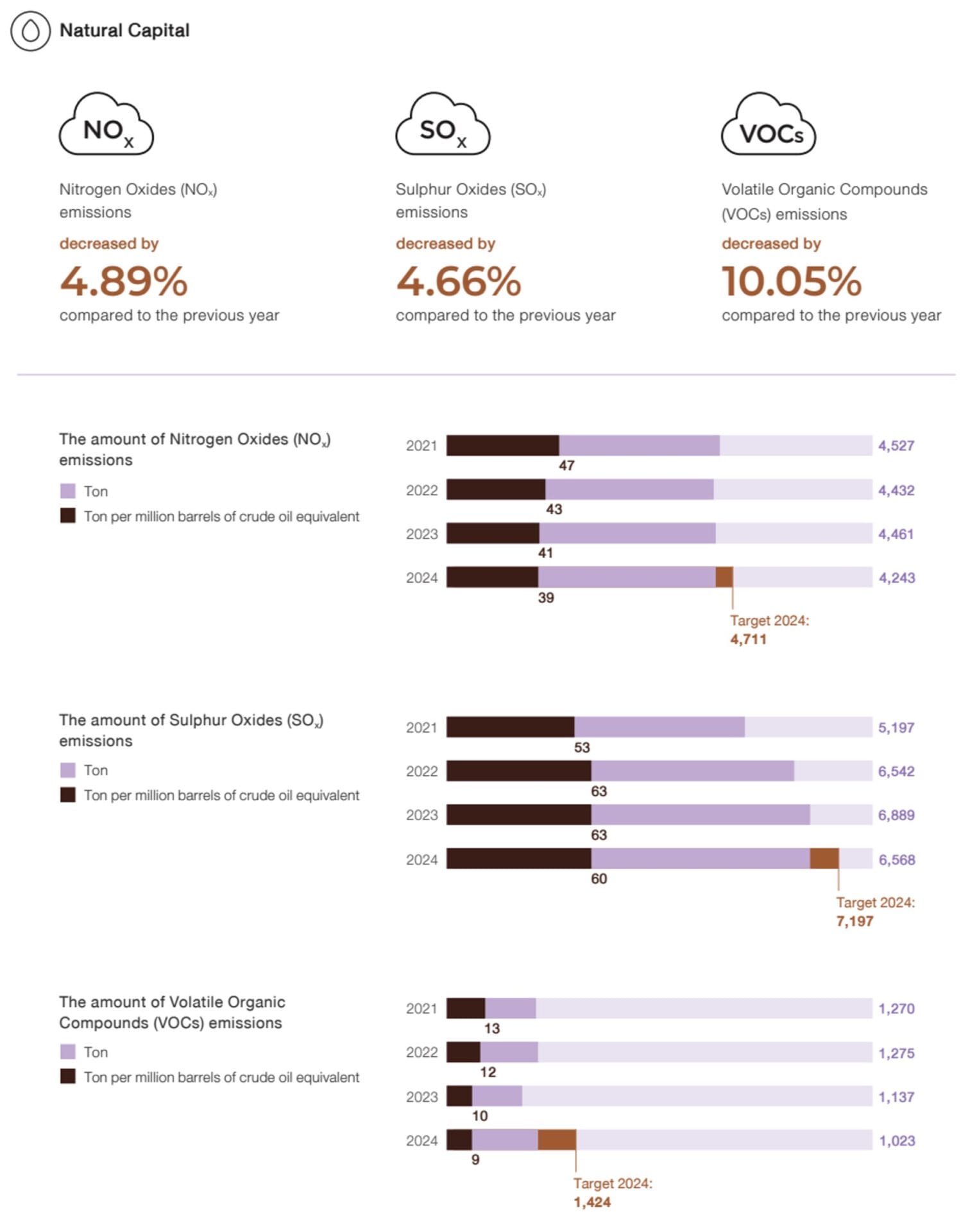